What is concrete made of? It’s a mix of three simple, yet essential ingredients: water, aggregate, and cement.
You might think, “Hey, that’s pretty straightforward!” But there’s actually a whole world of complexity lurking beneath the surface when it comes to crafting the perfect concrete blend. We’ve gotta be super picky about the amounts and qualities of these ingredients.
Now, these basic components team up to create the most adaptable material on Earth. So adaptable, in fact, that concrete takes the crown as the most widely used construction material across the globe.
Ready to dive into the nitty-gritty of concrete? Let’s uncover the magic of this “liquid rock” and reveal its hidden secrets!
What is concrete?
Imagine a liquid that magically hardens into a ridiculously strong, rock-like substance when it dries. That’s concrete in a nutshell!
First, let’s clear up a common confusion: cement and concrete are not the same thing. Cement is actually just a key ingredient in making concrete.
Concrete is a catch-all term for a bunch of different materials in the construction biz. It’s not a one-size-fits-all kinda thing, as some folks might think. You’ve probably heard of some popular concrete recipes like:
- Reinforced concrete
- Rapid-set concrete
- Asphalt concrete
- Portland Cement Concrete (PCC)
Each of these concoctions is designed for a specific use, making concrete a true jack-of-all-trades in the world of engineering. It’s the top choice for crafting jaw-dropping structures like roads, skyscrapers, dams, bridges, and other massive marvels.
So what makes concrete so popular? Check out this impressive list of features:
- Easily molds into any shape when freshly poured
- Super strong, durable, resilient, and long-lasting
- Can handle any environment
- Won’t burn, rust, or rot
- 100% recyclable
- Needs little maintenance
- Fire-resistant
- Insulates against vibrations and noise
- Doesn’t give off gases or toxic compounds when cured
- Wallet-friendly and easy to use
- Can be made locally
How is concrete made?
At first glance, concrete seems like a simple mix of paste and aggregates. The paste is made of cement and water, while the aggregate is a combo of sand and rock. But dig a little deeper and you’ll uncover the amazing complexities of this extraordinary material.
Before we dive into the details, let’s recap the basic ingredients of concrete:
- Water
- Fine aggregate (natural sand particles)
- Coarse aggregate (gravel, crushed stone, recycled concrete)
- Cement
- Optional: admixtures – special chemicals to tweak the mix’s properties
These ingredients are as down-to-earth as they come. Think about it: water falls from the sky, and the other bits are dug up from the ground.
Sure, cement—the heart and soul of the mix—takes a bit more effort to make. But this small snag doesn’t take away from concrete’s overall affordability and sheer awesomeness.
The best part? We’ll never run out of these ingredients, unlike other precious natural resources.
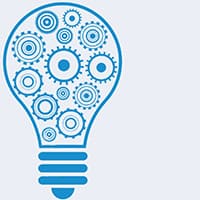
Important Note: Portland cement is the most common type of cement used in concrete. It’s a fine gray powder made by heating limestone and clay minerals in a kiln to form clinker. The clinker is then ground and 2% to 3% of gypsum is added.
The synergy of concrete ingredients
Let’s get down to the nitty-gritty: how do all the ingredients in concrete come together to create the sturdy stuff we rely on for our roads and buildings? The key player is cement!
But cement can’t go solo. It needs water to work its magic. When cement and water get together, a miraculous process called hydration kicks in. Tiny nodes sprout on the surface of cement particles, which then grow and link up with their neighbors. These nodes grab onto crushed rock and sand, creating a bond that holds everything together. It’s like putting together a jigsaw puzzle!
During this hardening process, a whole lot of heat is released. That’s because hydration is an exothermic reaction, or in plain English, “it produces heat”!
The really cool part is this: by measuring the temperature of your concrete, you can tell how far along the hydration process is. This technique, called measuring concrete maturity, helps you estimate the concrete’s compressive strength.
In short, when cement mixes with water, it creates a paste that covers the fine and coarse aggregate materials, acting like super glue. As this glue hardens, it forms the solid material we know and love, the stuff that supports our roads and buildings.
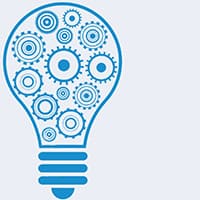
Important Note: Aggregates can be smooth or jagged. Smoother surfaces make concrete more workable, while rougher surfaces make it less workable but stronger.
In general, adding stones and sand to concrete boosts its strength. The cement bonds to the jagged edges of the stones, forming stronger connections that result in a tougher material.
The proportion of water and cement
As we’ve seen, water and cement team up to create an awesome paste. But to make the ultimate paste, you need to get the ratio of cement to water just right. That’s where the Water/Cement (W/C) ratio comes in.
The W/C ratio tells you the weight of water compared to the weight of cement in a mixture. The ideal W/C ratio depends on what you want to use the concrete for.
High-strength concrete requires a low W/C ratio. But you still need enough water to make the concrete workable so you can pour and mold it easily.
Watch out for adding too much water, or you’ll end up with a soupy cement disaster. In other words, you’ll dilute the cement paste too much, resulting in a weak material.
The W/C ratio is a big deal in every mix design. Even small changes in water content can dramatically affect your final product, impacting aspects like:
- Strength
- Workability
- Finished appearance
The proportion of aggregates and paste
The secret to a perfect mixture is all about balancing the ingredients.
If you use more aggregate than paste, you’ll end up with gaps in your mixture, leading to porous concrete and rough surfaces. But if you go overboard with paste, your concrete will cost more and be more prone to cracking.
Remember, aggregates help reduce shrinkage as concrete cures. Too much paste, and cracks will become more common.
In short, finding the right balance between aggregates and paste is crucial. Doing so will strengthen your concrete creation.
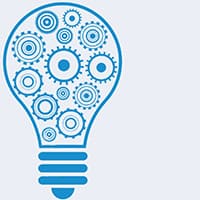
Important Note: The choice of aggregate depends on what you want to use the concrete for. This decision matters because aggregates can make up 60% to 80% of a mix design’s volume.
One example is a lean concrete mix, which uses only fine aggregates. This blend creates an affordable material that’s easy to remove.
Water choice
The perfect paste needs more than just any old water.
Using water full of impurities can open up a whole can of worms for your concrete, causing problems like:
- Efflorescence
- Nasty staining
- Delayed setting time
- Weakened strength and durability
- Corrosion of embedded materials
- Volume instability
In a nutshell, you want water with minimal chlorides, sulfates, alkalis, and solids. This means almost all drinking water should do the trick.
If you’re unsure about your water’s quality, give it an impurity test.
Admixtures for concrete
There’s a bunch of chemicals you can mix with cement, each designed for specific projects.
Before jumping in, make sure the additive is okay for your project. Here are the five most common admixtures you can add to your mix:
#1 Air-entraining agents: These marvels enhance workability, which is super important when dealing with freezing weather or when concrete is exposed to thawing, sulfates, and seawater.
#2 Accelerators: These agents speed up hardening, making them perfect for cold conditions. Pick between calcium chloride and non-calcium chloride varieties. But remember, calcium chloride accelerators are a no-no for concrete exposed to seawater, reinforced concrete, or concrete in contact with aluminum or other non-ferrous materials.
#3 Pozzolans: Make your mix more efficient by substituting or enhancing the cement, allowing for less usage while maintaining the desired concrete strength.
#4 Retarders: Use these trusty agents to control the setting time, especially handy for hot weather conditions to extend the hardening process.
#5 Water reducers: Get top-notch concrete quality by reaching the targeted material strength at lower water-to-cement ratios. These helpful additives also make your mix more workable.
What are the grades of concrete?
Concrete comes in a whole bunch of grades, each with unique strength and composition.
You’ll often see concrete grades labeled like “M5.” The “M” stands for mix, and the number 5 shows the concrete’s strength. This strength should be reached 28 days after pouring.
Strength is measured in MPa (megapascals) in the metric system and psi (pounds per square inch) in the imperial system. Both units represent pressure.
The ingredient mix ratio depends on the type of structure you’re building. This ratio includes:
- Cement
- Fine aggregate
- Coarse aggregate
Usually, you’ll find mix ratios in this format:
(1 : 5 : 10) means (1 part cement : 5 parts fine aggregate : 10 parts coarse aggregate)
Here’s a table that shows the main grades of concrete:
Grade of Concrete | Mix Ratio | Strength (MPa) | Strength (PSI) |
---|---|---|---|
Normal Grade of Concrete | |||
M5 | 1 : 5 : 10 | 5 MPa | 725 psi |
M10 | 1 : 3 : 6 | 10 MPa | 1087 psi |
M15 | 1 : 2 : 4 | 15 MPa | 1450 psi |
M20 | 1 : 1.5 : 3 | 20 MPa | 2900 psi |
Standard Grade of Concrete | |||
M25 | 1 : 1 : 2 | 25 MPa | 3625 psi |
M30 | Design Mix | 30 MPa | 4350 psi |
M35 | Design Mix | 35 MPa | 5075 psi |
M40 | Design Mix | 40 MPa | 5800 psi |
M45 | Design Mix | 45 MPa | 6525 psi |
High Strength Concrete Grades | |||
M50 | Design Mix | 50 MPa | 7250 psi |
M55 | Design Mix | 55 MPa | 7975 psi |
M60 | Design Mix | 60 MPa | 8700 psi |
M65 | Design Mix | 65 MPa | 9425 psi |
M70 | Design Mix | 70 Mpa | 10150 |
Conclusion
Concrete, one of the most adaptable materials known to us, is the backbone of our modern world.
Think about the amazing Roman Empire structures that still stand tall after nearly 2,000 years! In more recent times, the massive Three Gorges Dam in China holds back a mind-blowing 10.4 trillion gallons of water, while the stunning Burj Khalifa in Dubai soars to a jaw-dropping 2,717 feet.
What’s truly amazing is how simple concrete’s ingredients are. Yet, at the same time, concrete is incredibly complex, with mixtures needing some serious scientific know-how.
What do you think about this incredible material and its uses? Is there a more versatile material out there?