Good product design is far from easy, but by following my 7 mechanical engineering design tips, you can simplify the process.
Just so you know, I’m not a mechanical engineer by degree. Actually, I’m an electrical engineer, not that it really matters. I’ve just had my fair share of dabbling in mechanical stuff, and I’ve worked with some seriously talented mechanical engineers. So, I’ve got some solid, hard-earned wisdom to share.
Give these 7 tips a whirl, and who knows? Even a tiny improvement could make you a better designer. Then you can level up faster and work on even more awesome projects.
#1 Making your designs come to life in the real world
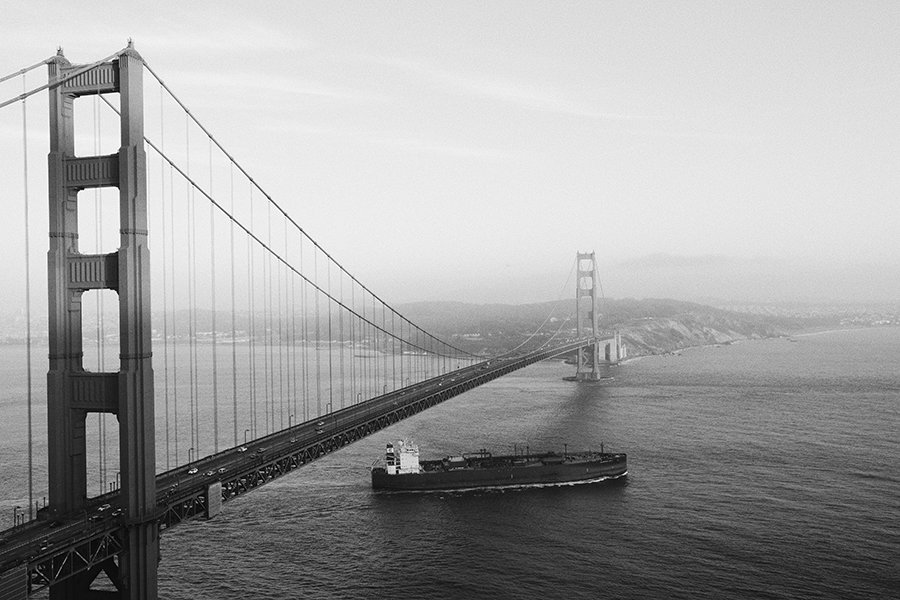
Sure, everything looks flawless on paper or CAD. But when you try to bring your design to life, that’s when the real fun begins. Almost every mistake you made rears its ugly head.
Imagine you’re designing a gizmo packed with electronic components. Forget just one component, and you’ll know something’s off, ’cause the gizmo just won’t work.
The takeaway? There’s no easy route to great design. A designer’s got to think about how their masterpiece will hold up in the real world. When I’m sketching out ideas, I put myself in the shoes of a contractor or manufacturer. Keep an eye on these things when you’re designing:
- Real-world practicality
- Math errors
- Safety factors
- Real-world variables
- Accuracy of information
- Challenges of construction and manufacturing
Poor designs can lead to all sorts of chaos:
- One tiny failure can bring down the whole design.
- Expensive change orders can blow the budget.
- Huge project delays can rack up financing costs.
- Undiscovered mistakes can cause injuries or even fatalities.
I’ve seen seemingly innocent assumptions throw entire projects off the rails. Just one example: I saw a pipe wrongly sized and installed underwater. The pipe was 50 feet below ground and stretched over a mile. That mistake put the project on ice and led to years of turmoil – not to mention a couple of engineers losing their jobs.
#2 Occam’s razor
If two answers seem equally likely, the one with fewer assumptions is probably the winner. That’s Occam’s razor in a nutshell.
In other words, keep it simple, folks. In your designs, start with the basics, and only add complexity if you really need to.
To pull this off, first define your problem as simply as you can. Then, find the simplest theory or framework that fits, and run with it. Your choice will set the tone for how simple or complex your design ends up being. Focus on simplicity in these areas:
- Design approach
- Design concept
- Component selection
Take the SpaceX Raptor engine, for example. Elon Musk didn’t reinvent the wheel. He just tweaked past full-flow staged combustion engines, aiming to make them better and simpler. Why? Because simpler engines make reusable rockets more practical. And on Mars, you don’t want to be fiddling with rocket refurbishments.
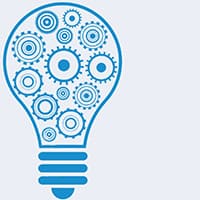
Important Note: Good design aims to minimize the number of components, which might mean using a few highly complex ones. But in the end, you’ll reduce the number of manufacturing processes.
It’s all about striking the right balance between component complexity and manufacturing processes.
#3 Focus on simplicity
Why am I diving back into the simplicity conversation? Well, it’s because simplicity is the backbone of any great design. Sure, a design has to function—that’s a given. But let’s be honest, we all crave more simplicity in engineering.
So, what does simplicity look like? In a nutshell, the easier it is to understand a design, the simpler it probably is. Makes sense, right?!
Take, for example, a widget that needs 10 different parts to operate. To fully grasp the design, you need to know how all these 10 parts work together. Now, imagine if there were only three parts…
Let me tell you, it takes a ton of creativity and know-how to reduce the part count. It’s far from easy. But that’s what sets great designs apart from the rest.
Moreover, many complexities remain hidden and out of sight for the end-user. To illustrate, consider a simple piece of PVC conduit you’d find at your local Home Depot. This conduit is complex, both scientifically and in manufacturing. But, it’s proven to work within a set of parameters. In other words, if you use it according to its specs, it won’t fail you.
In essence, the PVC conduit’s complexity is invisible to a design engineer. The designer just specifies a 3-inch conduit on a site plan without giving it much thought. That’s why it’s crucial to understand the source of complexities in your design. Not all complexities are inherently bad.
Now, let’s look at this example. What if the designer adds a bunch of unnecessary conduit bends and pull boxes to the design? The design will then undoubtedly become more complex. Construction and maintenance efforts will skyrocket.
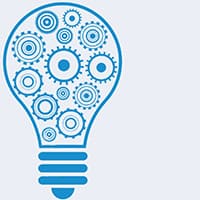
Important Note: There are four techniques that work well across industries to create simple designs. These techniques are:
- Add symmetry to designs
- Purchase third-party parts instead of making components from scratch
- Specify parts using industry standards
- Use proven, dependable designs as templates to iterate from
#4 Understand the laws of nature
It seems like every year, we’re delving deeper into the digital realm. But let’s not forget that we still live in the physical world.
So, it’s not surprising that most design engineers need to understand the physical world. For instance, you can’t design a bridge if you don’t know how wind affects your design. This is where creating small-scale physical models of your design comes in handy. You can test against the laws of nature before you commit to a design direction.
More often, though, engineers use simulation software to create models. The software incorporates all the mathematical models based on our understanding of the laws of nature. Without this analysis, design failures would be way more common.
Now, which laws of nature do we rely on? Some of the most common ones you’re probably familiar with include:
- Newton’s laws
- Maxwell relations
- Boltzmann equation
- Bernoulli’s principle
- Hooke’s law
- Lenz’s law
- Ohm’s law
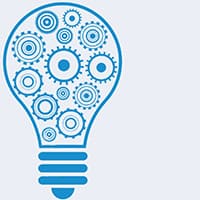
Important Note: A designer must understand the laws of nature. Otherwise, you’ll never catch those “gotcha” moments in your design, including incorrect outputs from software simulations.
The ability to spot such mistakes is where theory and real-world experience intersect. And if you ever aspire to be a 10x engineer, you’ll need both to succeed.
#5 Abbe’s principle
Abbe’s principle, which states, “Maximum accuracy is obtained when the scale and the measurement axes are common,” can be broken down into three easy-to-understand rules:
#1 To achieve the best results, take linear measurements as close to the action as possible. Like, if you’re measuring the water in a pot, put your measuring device right in there with the water instead of a foot away.
#2 If you can’t take a linear measurement, at least try to measure parallel to the line you’re trying to measure.
#3 If you can’t maintain parallelism between the part and the measurement, you’ll end up with an error. This error, called Abbe’s error, increases as the angle between the measurement and the part gets bigger, and as you move the part further from the scale.
So, when designing stuff, keep parts close to the process they’re involved with. Otherwise, you’ll end up with bigger measurement errors. This applies to all sorts of measurements, like temperature, pressure, voltage, current, and flow.
A perfect example of what happens when you don’t maintain parallelism is a spinning top. If you bend the axis a little, the top will wobble. Bend it more, and it wobbles even more. This wobble is Abbe’s error, also known as sine or cosine error.
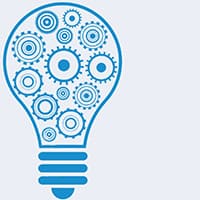
Important Note: Build manufacturing machines as precisely as possible. For example, assembly line guideways and beds should be super uniform and maintain a consistent temperature. Otherwise, your measurements will be off, and your tolerances will suffer.
#6 Keep functions independent
Do your best to keep your design’s functions separate from one another. Break down complex designs into simple, individual functions. Take an airplane, for instance – you can break it down into:
- Power plant
- Empennage
- Landing gear
- Fuselage
- Wings
And then, you can break down each of these parts even further. Like the power plant:
- Electrical infrastructure
- Engine
- Control and instrumentation
- Fuel system
I get it – it’s easier said than done, especially with all the interdependence between parts. But starting with separate parts in the design phase helps you focus on creating the best possible components, and it’s a more logical approach given the specialized skills needed for each part.
#7 Identify sensitive directions and reference features
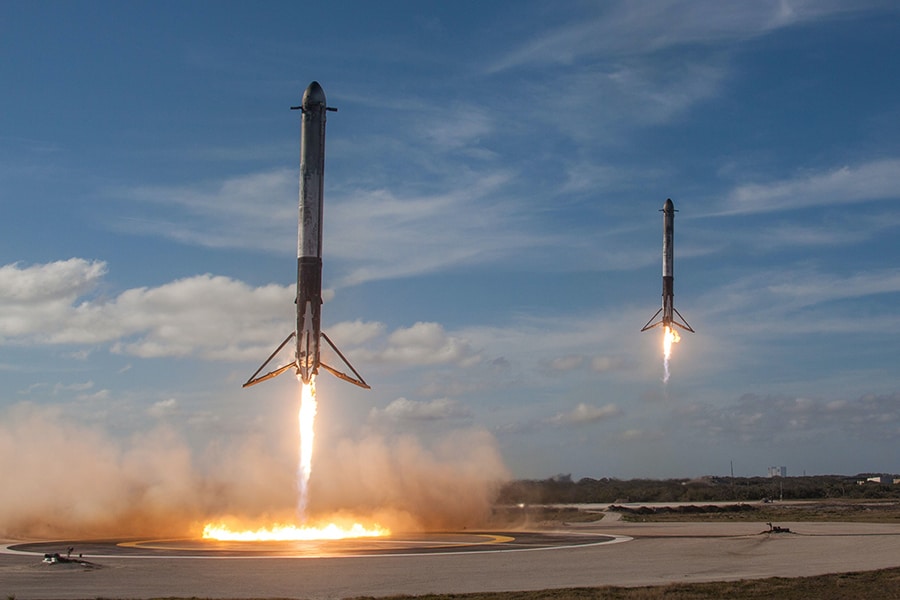
Every design has that one aspect or component where precision and consistency are absolutely vital.
Imagine a SpaceX rocket landing on a floating drone ship. The rocket needs incredible accuracy as it descends, collecting data constantly. So, the critical component here would be the sensors on the rocket.
If there’s a glitch in data collection during descent, the rocket might not have time to correct its course and could end up in the ocean.
That’s why it’s essential to spot the critical areas in your machines and invest extra elbow grease to ensure accuracy in those key spots. Don’t forget to maintain precision where it matters most.
Additionally, recognize the indispensable features that remain constant in your design. These are the elements you simply can’t do without. Make sure to build your design around these fundamental features.
Mechanical engineering design tips wrap up
Design work demands a ton of effort, but creating fantastic designs requires even more. After all, the best designs appear deceptively simple at first glance. But, as always, the devil’s in the details.
Employ these mechanical engineering design tips to take your work to the next level. You’ll soon be crafting more practical and cost-effective designs, setting yourself apart from the average engineer.
Which mechanical engineering design tips do you find the most useful? What challenges do you face when it comes to design work?