In this electrical conduit guide, I’m gonna walk you through different conduit types, their uses, and share some handy installation tips.
I’ll cover these four popular conduits:
- EMT (Electrical Metallic Tubing)
- GRC (Galvanized Rigid Steel Conduit)
- FMC (Flexible Metal Conduit)
- PVC (Polyvinyl Chloride)
Remember, electrical conduits can be either rigid or flexible, and they come in various materials like metal, aluminum, PVC, or steel. The key is to pick the right one for your installation, which will simplify the process and reduce maintenance.
Before we dive into each conduit type, I’ll share some general tips and tricks I’ve picked up from years of working on all kinds of engineering projects. These tidbits apply to both industrial and residential settings.
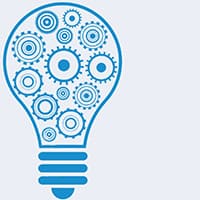
Important Note: Always use the latest National Electrical Code (NEC) for any electrical work. It’s your go-to guide for code-compliant installations. Don’t forget to check with your local building department for any locally enforced codes, too!
General conduit tips for every project
Tip #1: Sketch it out
Before you even think about grabbing your tools, draw a conduit plan to help you:
- Determine the type and length of conduits needed
- Assess the practicality of your design
- Figure out junction box placements
- Avoid damaging existing conduits and piping underground
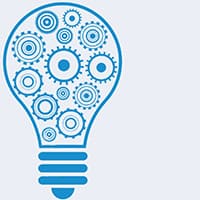
Important Note: Call your local utility company and dial 811 to locate buried pipes, so you don’t accidentally hit a gas or electric line.
Tip #2: Conduit sizing
Choose the right conduit size based on the number of wires running through it. Consult NEC Chapter 9, Table 1 as your guide:
Number of Conductors in Conduit | Maximum Fill Allowance |
---|---|
1 | 53% |
2 | 31% |
Over 2 | 40% |
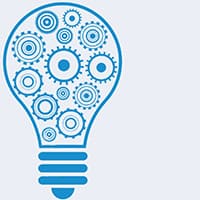
Important Note: For long conduit runs, bump up the size by one. This makes installation and maintenance a breeze, especially with a few 90° bends in your run. Also, stick to a minimum conduit size of 3/4 inches for easier wire pulling.
Tip #3: Limit conduit bends
NEC 358.26 restricts the total number of bends to 360° between pull points. I recommend keeping directional changes under 270° to simplify installation and future maintenance, particularly when pulling large conductors.
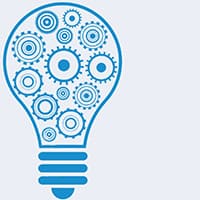
Important Note: Avoid bends and offsets when possible. Use fittings for turns, and resort to an approved hickey or conduit bending machine only when necessary.
Tip #4: Use conduit supports
Secure all conduits and fittings on exposed surfaces using clamp backs, channels, or struts. Follow the National Electrical Code for conduit support spacing, and never exceed 4 feet. Check out NEC 358.30 for more info.
Tip #5: Use conduit fittings
Unthreaded fittings come in two main types:
- Gland (compression) type
- Set-screw type
Remember, the gland type is your go-to for wet locations.
In dry spots, connect your conduits using threadless set-screw couplings. Slide the end pieces of the conduits into each side of the coupling, then tighten with set screws.
Here are some other fittings worth using and why:
- Expansion fittings: Perfect for places with big temperature swings, as they help limit stress damage from expansion and contraction.
- Ground fittings: Use these where conduit breaks happen to maintain ground continuity by creating a jumper path around any interruptions.
- Elbows: For those 90° conduit direction changes.
- Drain: Install these in areas with temperature swings where condensation might occur. Pop a drain at the lowest point of a conduit run, where water may collect.
Tip #6: Opt for pre-bent conduits and fittings
Using pre-bent conduits and fittings saves you time and effort, plus ensures better quality control. Try to do as little self-bending as possible to avoid damage.
Tip #7: Cutting and reaming conduits
You can cut some conduits using a hacksaw. But always remember to ream and smooth the edges afterward. Sharp conduit edges are bad news for pulled wires.
Tip #8: Failsafing wall and roof conduit penetrations
- Install wall seals for all conduits going through walls.
- Put in expansion and deflection fittings where conduits cross building expansion joints.
- Keep roof penetrations watertight with weatherproof hot-dipped galvanized sheet metal flashing caps.
Tip #9: Ideal underground and aboveground conduit types
For long-lasting installations, stick with these conduit types:
Underground: Go for nonmetallic Schedule 40 high-impact PVC for underground conduit installations. Make sure they’re UL approved for direct burial or concrete encasement. For fittings, use PVC solvent weld type.
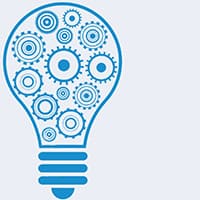
Important Note: Use PVC coated GRC for underground to aboveground 90° elbows and risers. Read more here.
Aboveground: Rigid steel conduits are your best bet for aboveground installations. They should conform to ANSI 1 C80.1. Don’t forget to apply zinc coating to the inside and outside of the conduit by hot-dip galvanizing after threading.
Tip #10: Make your exposed conduit raceways look sharp
Run conduits on exposed surfaces at right angles to, and/or parallel to, surrounding walls. Make sure exposed conduit runs follow the form of ceilings.
EMT (Electrical Metallic Tubing)
What is EMT? It’s not exactly a conduit, but a tubing.
Though you can thread EMT, you’ll typically assemble it using couplings and connectors. Connect conduit pieces with set screws or compression glands for a budget-friendly, quick, and simple installation compared to threaded metallic conduits.
Where should you use EMT? It’s usually for indoor use only. It’s too thin for underground installation and can easily get damaged. So, keep EMT above ground!
Even indoors, avoid installing EMT where it could get physically damaged. Ideally, use EMT in these spots:
- Inside walls
- In offices and corridors
In these locations, EMT is a better choice than GRC (which we’ll discuss next) just because it’s easier on the wallet.
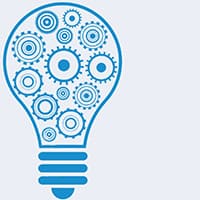
Important Note: When you can, make sure to color code the EMT inside your building. Go for different colors for 480V, 120V, and 24V wiring – it’ll make maintenance a breeze.
GRC (Galvanized Rigid Steel Conduit)
What is GRC? Picture a thick wall conduit with threaded ends that can be coupled with threaded fittings, or even go threadless. In simpler terms, Rigid Metallic Conduit (RMC) is a generic term, and GRC is a specific one. Most people just call RMC “rigid.”
You can find steel, stainless steel, and aluminum RMC out there, but GRC is the most common one, and it’s the galvanized type.
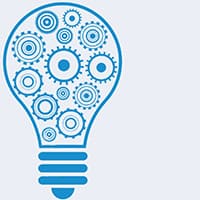
Important Note: You can find metal conduits made of aluminum and stainless steel. But remember, when you see “GRC” on a spec, it specifically means galvanized rigid conduit.
Now, if the spec says “RMC,” things get a bit murky. RMC isn’t always galvanized steel, but all rigid galvanized steel conduit is RMC.
Where should you use GRC? It’s perfect for indoor use in almost all locations, thanks to its durability. You’ll find it in most industrial facilities. GRC is also great for outdoor use above grade, but I wouldn’t recommend it for underground or highly corrosive areas. Even zinc-coated galvanized RMC may not provide enough protection in some cases.
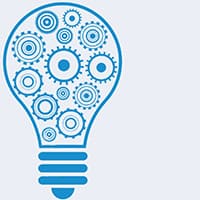
Important Note: Intermediate Metal Conduit (IMC) has the same outer diameter as RMC, but its wall is thinner. This makes IMC a little weaker, but there’s more space inside for wire pulling.
Flexible Metal Conduit (FMC)
What is FMC? FMC, or “flex,” is helical coiling used indoors, made from interlocked steel or aluminum strips. You can pull wire through it and bend the tubing however you like.
For outdoor use, go for Liquidtight Flexible Metal Conduit (LFMC). It’ll keep your wires and cables dry and safe from moisture.
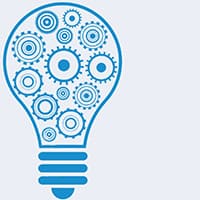
Important Note: FMC and LFMC are perfect for vibrating equipment. For example, a pump motor should have a flex connected to it, because a rigid conduit might snap.
PVC (Polyvinyl Chloride)
What is PVC? It’s a rigid nonmetallic conduit with the same perks as RMC. Plus, you can use it in wet or corrosive environments.
PVC has the following advantages:
- Lightweight
- Durable
- Strong
- Easy to cut
- Corrosion-resistant
However, watch out! PVC can get brittle when it’s cold and saggy when it’s hot.
Where should you use PVC? Almost everywhere, really. It’s resistant to heat, fire, and sunlight. In fact, there’s no better choice than PVC Schedule 40 for underground use. But for risers, if damage could happen, go with PVC Schedule 80.
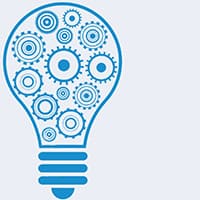
Important Note: PVC Schedule 40 and PVC Schedule 80 are super similar. However, Schedule 80 has a few differences:
- Thicker walls
- Smaller inside diameter
- Heavier weight
Electrical conduit guide wrap up
Knowing your conduits inside and out is crucial for any electrical project. It’s the key to a smooth installation and hassle-free maintenance down the line.
Which conduit type do you use most often? And what’s got you scratching your head when it comes to picking the right conduit?
Since you recommend using PVC conduit for underground applications, do you stay with PVC all the way to the aboveground electrical boxes or do you transition to metal conduit once you are above ground?
Above ground, you transition to GRC. To point out, typically, you want the transitional portion of the conduit from underground to aboveground (e.g. the 90s and riser pipes) to be PVC-coated rigid. After this transition segment, you can just use GRC to your electrical box.
Is there a standard for when to use steel vs. stainless steel, or aluminum RMC or can you give information as to the benefits of either?
Many different pros/cons. To touch on the subject…
Use only stainless steel conduit, when chemically compatible, in all areas that are or could be in contact with corrosive chemicals (sulfur dioxide, caustic, fluorides, or others). These conduits can take a lot of abuse, but they’re expensive – both in material and labor – cutting and threading stainless steel rigid is not easy. This is why you rarely find stainless steel installed in the field.
Stainless steel is not compatible with chlorine (bleach), bleach will corrode and eat up stainless steel, use PVC in those cases.