The SpaceX Raptor engine is taking engineering to new heights, with every aspect of these monstrous engines being absolutely mind-blowing!
We’re about to dive into the engineering side of these fascinating engines but don’t worry, we won’t get too deep into the technical stuff. Trust me, though, the overview I provide will be enough to make you realize just how astonishing and amazing these engines are.
But, hold on a sec! Before we go any further, we need to lay some groundwork. To truly appreciate what we’re about to discuss, you’ll need a basic understanding of rocket science. Specifically, you should know how two substances enter a combustion chamber in a controlled manner. Don’t sweat it, though, these super cool and easy-to-understand videos have got you covered:
- Basics of how rocket propellants in a gas-generator power cycle work by Lescis.
- A detail of how rocket propellants and rocket engine plumbing work by Scott Manley.
- Overview of how full-flow staged combustion rocket engines work by Scott Manley.
Feeling ready? Alright, let’s dive headfirst into the awesomeness and get down to the nitty-gritty!
The SpaceX Raptor engine overview
The SpaceX Raptor engine is one of just a few full-flow staged combustion cycle engines in the world – and that includes the entire history of rocket engineering! And what’s even more jaw-dropping, SpaceX is pushing the boundaries of what we thought was possible.
Developing and manufacturing these rocket engines in-house, SpaceX is super agile, testing, failing, tweaking, and repeating like a software-based startup.
But that’s not all! These Raptor engines have a crucial job to do – they’ll power the SpaceX Starship to Mars! So, yeah, these engines need to be mighty powerful and super reliable.
Curious about the evolution of the SpaceX Raptor engine? Check out the table below for a timeline of all their incredible achievements.
Date | Description |
---|---|
October 2012 | SpaceX publicly announces concept work on rocket engine that'll be "several times as powerful as the Merlin 1 series of engines, and won't use Merlin's RP-1 fuel." |
November 2012 | Elon announces a new direction for the propulsion division of SpaceX, with the development of methane-fueled rocket engines. |
Early 2014 | SpaceX confirms Raptor engine will be used for the main Mars Colonial Transporter. |
May 2014 | Raptor engine component testing begins (e.g. testing on Raptor injector elements). |
April to August 2015 | SpaceX does 76 hot fire tests of a full-scale oxygen preburner. |
January 2016 | US Air Force awards SpaceX $33.6 million to develop a prototype version of its methane-fueled reusable Raptor engine. |
Early 2016 | SpaceX constructs new engine test stand at their McGregor test site in Texas for Raptor engine testing. |
August 2016 | First integrated Raptor rocket engine completed and shipped to McGregor test site for development testing. |
September 2017 | SpaceX completes testing with 200 bars (2,901 psi) combustion chamber pressure using new SpaceX created SX500 alloy. |
February 2019 | First test flight (lasted 2 seconds) of Raptor engine with combustion chamber pressure of 170 bars (2,466 psi). |
June 2020 | Raptor engine achieves a combustion chamber pressure of 300 bars (4,351 psi) on a ground test. |
August 2020 | Raptor engine achieves a combustion chamber pressure of 330 bars (4,786 psi) on a ground test. |
February 2021 | Starship prototype SN9 launched to an altitude of 10km and is destroyed on landing. |
May 2021 | Starship prototype SN915 launched to an altitude of 10km and successfully lands back on pad. |
There’s still a lot of work to be done on both the engine and its integration with the Starship, but what’s been accomplished so far is nothing short of amazing! And that’s a perfect segue to explore what all the fuss is about with these engines. To kick things off, let’s compare the Raptor engine to the gas-generator rocket cycle engine.
The gas generator cycle engine overview
The gas-generator cycle engine, also known as an open cycle, is super common. It’s probably one of the most widely used liquid-fueled rocket engines for orbital rockets. Here are some examples of where they’re used:
- F-1 rocket engines on the SpaceX Falcon 9 second stage
- F-1 rocket engines on the Saturn V booster stage
The schematic below gives you a simple, stripped-down idea of how the engine operates.
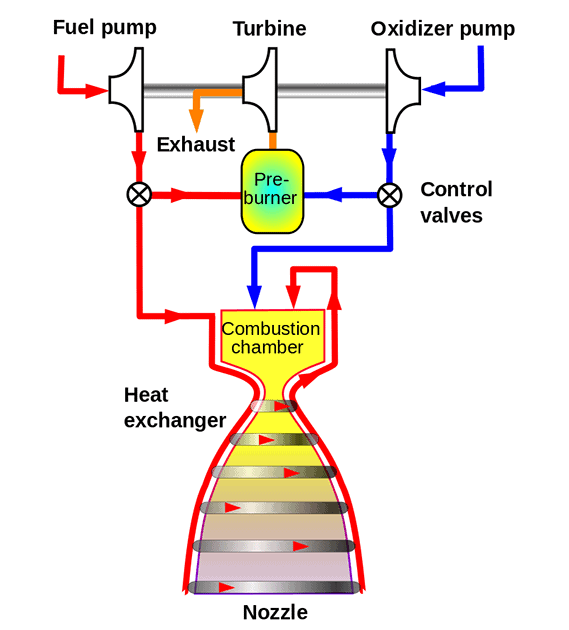
In a nutshell, we want to drive loads of oxidizer and fuel into the combustion chamber (check the blue and red lines pointing to the top of the chamber in the schematic). Simultaneously, we want to maximize the pressure in this combustion chamber to achieve maximum thrust. So, engineers need to design around this requirement while considering that pressure flows from high to low in engines.
And how do they do this without a highly pressurized propellant tank? With a rockin’ turbopump system, of course!
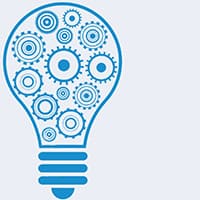
Important Note: The turbopump system is made up of two pumps, a turbine, and a mini rocket engine (aka a preburner or gas generator). And there’s a single shaft connecting the turbine to both pumps.
The burner gets the turbine going, and the pumps, acting as loads on the turbine, deliver a massive amount of fuel and oxidizer to the combustion chamber. In a nutshell, the rocket transforms the propellant’s chemical energy into kinetic energy.
It’s no wonder that turbopumps work at a higher pressure than the combustion chamber. The burner’s inlet is the highest pressure point in the whole engine, and the pressure decreases as you move downstream. Keep an eye out for a schematic later in this article that shows the various pressure values in an engine’s cycle.
Did you notice the taps connecting the main fuel and oxidizer lines to the burner in the schematic? Only a small amount of fuel and oxidizer enters the burner to generate gas for the turbine. The turbine then powers the incredibly strong pumps, and the combustion chamber gets flooded with highly pressurized propellant. It’s kind of like a never-ending domino effect.
Now, let’s talk about the part labeled “Exhaust” on the schematic. Here’s our catch-22: at this point, the highly pressurized unburnt propellant from the turbine is dumped overboard.
Not surprisingly, engine efficiency takes a hit because of this exhaust. You’re wasting some high-pressure propellant that could’ve entered the combustion chamber to help maximize rocket thrust.
As we’ll learn, increasing propellant flow through the combustion chamber boosts thrust. And the more pressurized and hot the propellant is (to a certain extent), the better. But hold your horses. The open-cycle design has its limits:
- A cap on the amount of propellant flow
- A cap on how pressurized and hot the burner can get
- Sooting due to unburnt fuel leaving the burner exhaust
These limitations make the engine less suitable for heavy-load applications. And this sets the stage for our full-flow staged combustion engine discussion. But before we dive in, let’s take a mathematical look at these limitations.
The mechanical power to drive the pumps
Here’s the equation that shows what we need:
Where,
= mechanical power to drive the pumps
= oxidizer flow rate
= fuel flow rate
= pressure rise in oxidizer pump
= pressure rise in fuel pump
= oxidizer pump efficiency
= fuel pump effficiency
= oxidizer density
= fuel density
So, to give a boost, we need to up the propellant flow rate or increase the pressure. But as we discovered, there’s a cap on how much we can crank up these variables.
Push too high, and we’ll guzzle fuel and run into soot trouble. Crank up
and/or
too much, and we risk torching the turbopump. No wonder these engines aren’t cut out for heavy payload applications!
Keep these relationships in mind, as we’ll circle back to them when discussing the awesomeness of the full-flow staged combustion engine.
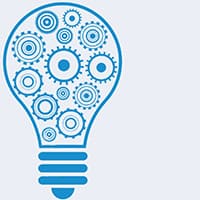
Important Note: To keep temperatures in check, you adjust the fuel-to-oxidizer ratio. Going too hot will wreck your turbine and pumps, so you can either add more fuel (fuel-rich) or more oxidizer (oxidizer-rich).
Running a fuel-rich engine with RP-1 fuel, you’ll quickly see unburnt fuel as dark clouds of soot coming out of the burner exhaust. This sticky soot can cause damage to all those moving rocket parts.
So, engineers control the turbopump temperature with fuel-rich oil. Since you can’t bump up the oxidizer, your only choice is to add more RP-1. But then you get more soot and waste fuel, so you gotta dial back engine operations to stay on the safe side.
Don’t forget, there’s a risk in having the two pumps share a common shaft. If oxidizer leaks through the seal into the fuel pump—BOOM!
The full-flow staged combustion cycle engine overview
Now let’s get to the amazing full-flow staged combustion cycle engine, also known as the full-flow closed cycle.
Just a side note: There were other engine designs between the open cycle and the full-flow closed cycle, but for the sake of brevity, we’re skipping those.
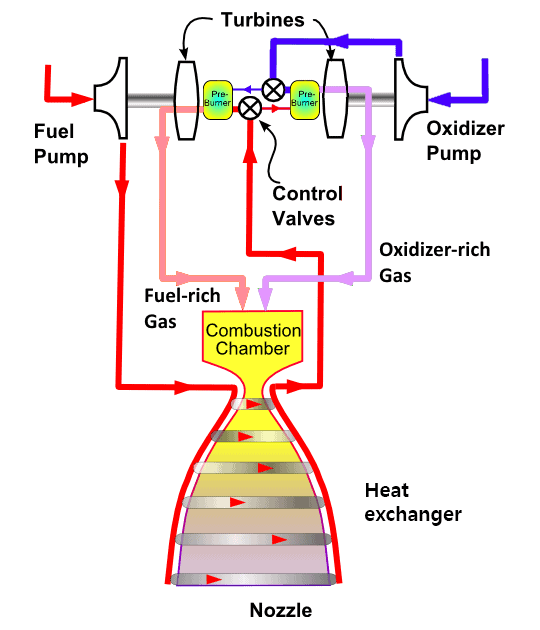
In this engine, the propellants burn in stages, and there are two preburners instead of just one. One is fuel-rich, and the other is oxidizer-rich. The fuel-rich preburner powers the fuel pump, while the oxidizer-rich preburner powers the oxidizer pump. Sounds like the perfect design, right?
In the schematic, you’ll see the fuel-rich preburner taps off the oxidizer flow. Lots of fuel passes through, but very little oxidizer, and vice versa for the oxidizer-rich preburner. This gives us mostly unburned, vaporized propellant—which is exactly what we want!
The hot gases spin their respective turbines and drive their pumps, just fast enough to optimally pressurize the preburners and, in turn, the combustion chamber.
The magic happens when the fuel and oxidizer arrive in the combustion chamber as hot gas, which means hotter temperatures and better combustion. The propellant burns twice: first in the preburners at lower efficiency, just enough to spin the turbines at the ideal speed, and then in the combustion chamber at max efficiency for maximum thrust. Best of all, no propellant goes to waste!
This engine is perfect for high-power rocket applications, like SpaceX Raptor engines, which can climb Earth’s gravity well more easily.
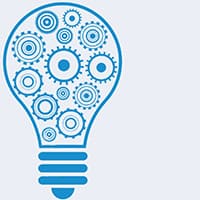
Important Note: SpaceX’s Raptor engine tech isn’t exactly fresh out of the oven. Others have crafted and tested similar engines before. But they never made it to production or test flights, thanks to a heap of engineering challenges.
For one, getting the two turbopumps to start in sync is a complex feat, demanding a sophisticated feedback and control system. Then there’s the issue of high-temperature piping for hot gas flow, especially in the oxidizer-rich cycle. Engineers need materials that won’t crumble under oxidization or melt when the engine’s fired up.
SpaceX’s metallurgy squad whipped up a super alloy, SX500, to fend off oxidization. Plus, they plonked their oxidizer turbopump right on top of the combustion chamber, minimizing the metal exposed to the flow of rich oxidizer.
Maximizing total power output with a Raptor engine
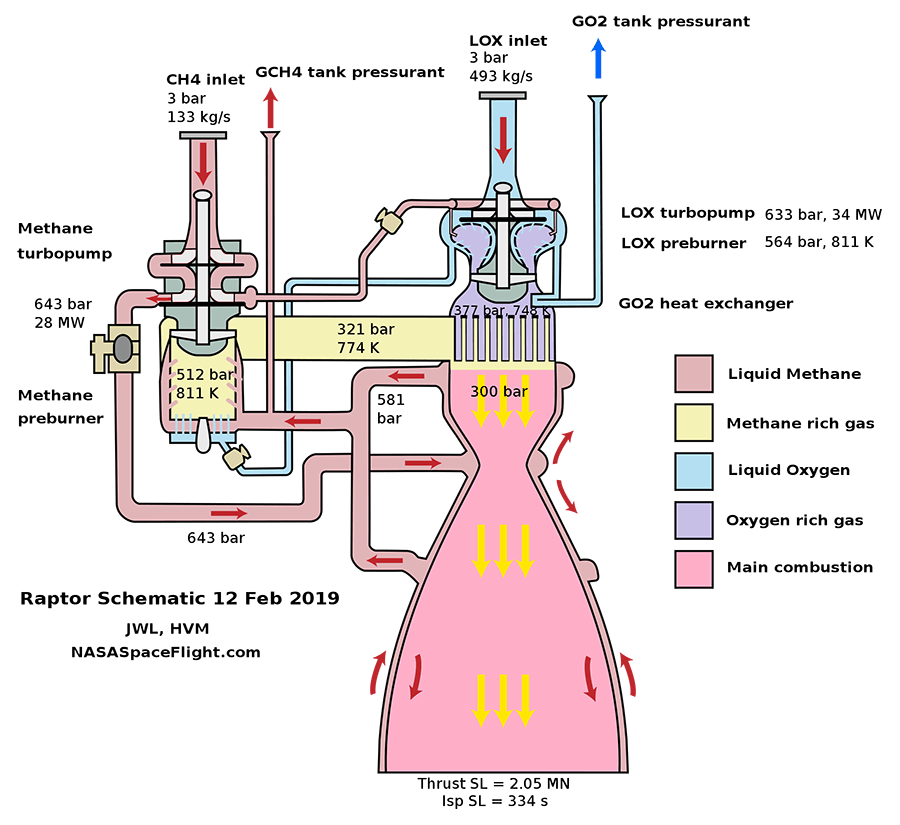
Let’s dive into the nitty-gritty of this engine’s applications.
First off, we’ve got nearly double the mass flow entering the combustion chamber, thanks to two turbines in the full-flow schematic rather than one. So there’s a boatload of propellant coursing through the preburners, letting us optimize preburner outputs for the perfect turbine speed.
Now brace yourself for this pleasant surprise: as we ramp up the thrust, our precious turbines and pumps remain safe and sound, without any temperature or pressure spikes!
Let’s rewind to the open-cycle engine operation for contrast. In the open-cycle, you use as little oxidizer and fuel as possible in the burner, as some fuel gets dumped overboard, and the cost per kilogram of cargo to space is sky-high. We’re talking a whopping $2,720/kg, as advertised by SpaceX for the Falcon 9. And if you use RP-1, you’re in for soot issues.
So, the burner runs at the highest temperature allowed by the turbine specs to prevent a meltdown. But that’s not all; thermal stress on the turbine blades causes the material to weaken.
Sadly, this is the only way to max out efficiency at a reduced flow rate. To better explain with math, let’s look at NASA’s turbine thermodynamics:
TW =
TPR =
Take note of the following variables,
TW = the turbine work per mass of airflow
TPR = the turbine pressure ratio
Tt = total temperature at turbine entrance
Tt = total temperature at turbine exit
pt = total pressure at turbine entrance
pt = total pressure at turbine exit
= specific heat ratio
As we crank up the inlet temperature to the burner, the turbine efficiency increases. But hold up, pushing the temperature of the turbine to its limits is a big no-no, as we just discussed.
Enter the full-flow closed-cycle engine, which dodges all these issues without a spike in temperature. Why? It’s all thanks to the fuel and oxidizer flowing through the preburners. This way, you can burn just enough propellant to max out turbine efficiency. Remember that equation for mechanical power we chatted about, which hinged on the flow rate? That’s the golden ticket!
So let’s break it down. The Raptor engine boasts these killer advantages over the open-cycle engine:
- Increased mass flow rate
- Separate fuel-rich and oxidizer-rich mixtures
- Dedicated turbines for the fuel-rich and oxidizer-rich mixtures
- Plumbing for all propellant to flow from the turbines to the combustion chamber
- Use of liquid methane versus RP-1 or hydrogen for fuel, keeping soot in check
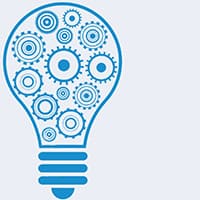
Important Note: There’s a tradeoff between efficiency and complexity. Using two gas generators allows for more relaxed turbine requirements. The load to achieve max power gets spread over two power sources instead of one. In return, the turbines can operate at a low, non-destructive temperature. But remember, with two turbines, the complexity and potential failure points go up.
Maximizing specific impulse with a Raptor engine
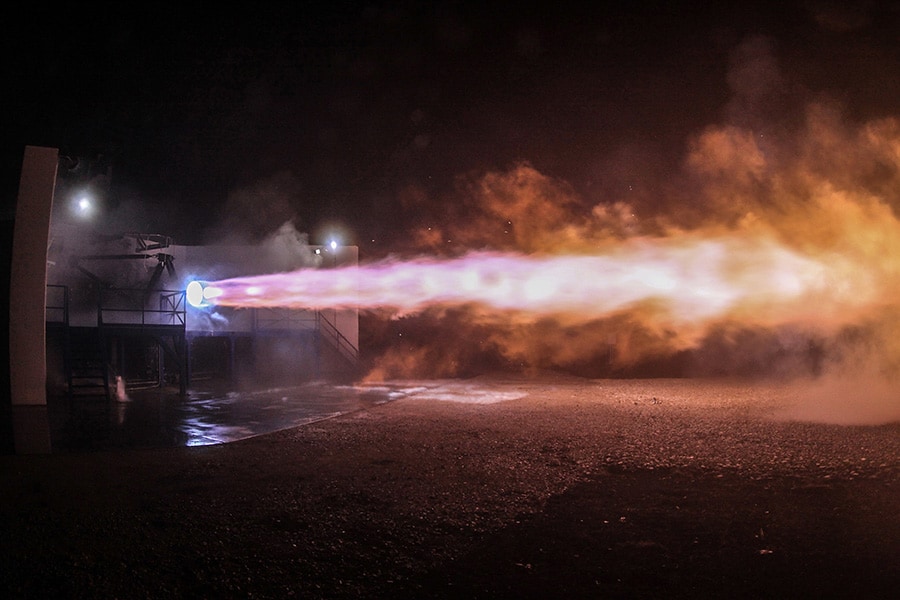
The increased total power output makes the SpaceX Raptor engine a beast. To show you what I mean, let’s circle back to our turbines and pumps for a quick physics refresher.
With the turbines running at optimal levels, the high-powered pumps generate insane pressure. The produced turbine power is nearly equal to the volume flow multiplied by the pressure drop across the turbine. The simple math relationship for calculating power in watts is:
Volume flow x Pressure drop =
Where watt =
So, as more mass gets pushed through the rocket engine, combustion chamber pressure rises. This then leads to greater exhaust velocity and thrust. We can illustrate this relationship using the following equation too:
C* is the characteristic exhaust velocity, which measures the amount of energy available from the combustion process. Meanwhile, represents the combustion chamber pressure.
Now, you’re probably wondering where specific impulse fits into all this, right?
Before diving into that, let’s chat about specific impulse. It’s measured in seconds, which sounds weird, I know. But it’s actually simple if we reframe the definition.
Think of it as the time in seconds a given fuel weight onboard a rocket will produce a constant amount of thrust. So, if a rocket has 100 pounds of thrust with a specific impulse of 200 seconds, it’ll burn 100 pounds of fuel every 200 seconds. Basically, it’s a measurement of how efficiently a rocket uses its fuel, kind of like your car’s fuel economy when driving at the sweet spot of X mph.
Let’s jump back into the mix. Here’s the relationship between specific impulse () and C*:
C* captures the essence of combustion, where is the thrust coefficient for the nozzle impact. So, with
= 1, C* =
.
You might be wondering, what do these fancy equations mean in the end? Well, it means the SpaceX Raptor engine can lift a whole lot of weight out of Earth’s gravity well.
Physical space-savings with Raptor engines
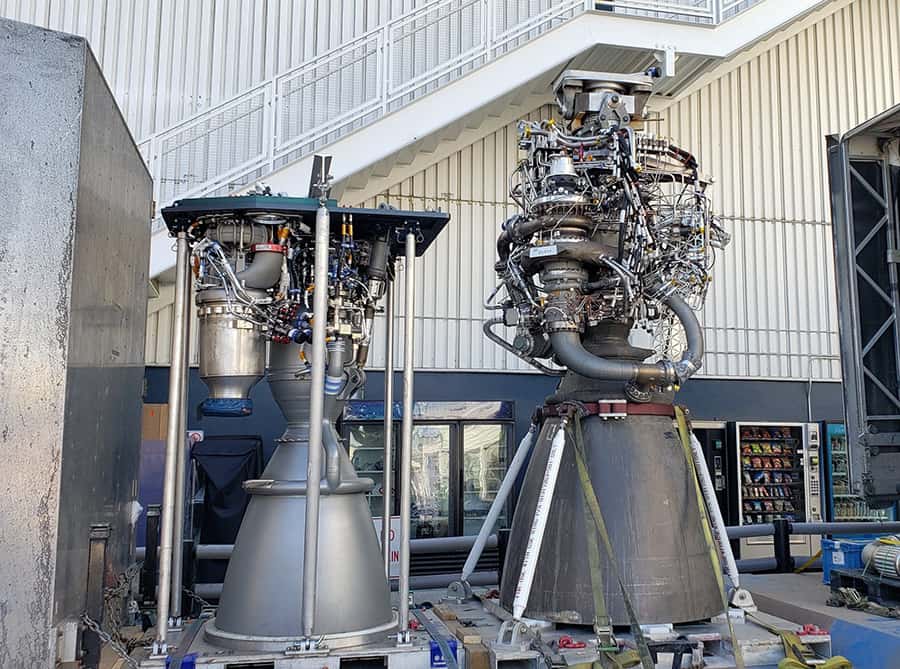
With a high specific impulse, you score some serious space-saving perks. You can squeeze more engines into the same area that used to fit just one engine. That means you get way more oomph for your buck with a Raptor engine.
For instance, you can cram four Raptor engines into the same space that used to house one Space Shuttle Main Engine (SSRE). Say goodbye to needing Solid Rocket Boosters (SRB) for that extra push. You’ll save on costs and boost safety—talk about a game-changer!
According to Elon Musk, the Super Heavy, the booster designed to push the Starship,
Will have 31 engines, not 37, no big fins and legs similar to ship. That thrust dome is the super hard part. Raptor SL thrust starts at 200 ton, but upgrades in the works for 250 ton.
You couldn’t dream up the same thrust specs using any other existing engine. If you tried, you’d end up with a ludicrously massive and impractical rocket.
What’s more, the high engine count gives you a safety net. So if you lose an engine or two, you’re still good to go. In fact, you could lose 6 Raptor engines and still, in theory, make it into orbit. Keep in mind, though, the Starship specs aren’t set in stone, so a lot of this is speculative.
But let’s keep rolling. Most SpaceX engines steer using gimbaling. With a gimbaled thrust system, you can swivel your rocket’s exhaust nozzle side to side. This gives you control over the direction of the thrust relative to the rocket’s center of gravity.
The big deal here is that if you lose an engine on the rim of the rocket, all hope is not lost. You can tweak your thrust vector directions to compensate and stay on course. This backup plan is something you don’t want to be without when you’re zooming to low Earth orbit at 17,600 mph.
Reusability of a Raptor engine
We’ve seen that with gas-generator cycle engines, leaks can be a problem. Oxidizer might sneak into the fuel pump from the seal on the shaft. That’s because everything in the engine is basically connected in a big circle, with components relying on each other.
But with the Raptor engine, the oxidizer-rich side only deals with oxidizer, and the fuel-rich side is all about fuel. The two sides aren’t connected. So if hot fuel leaks through the seal on the shaft and enters the fuel pump, it’s not a big deal.
Also, seals in gas-generator cycle engines can take a beating even in successful launches due to leaks. So it’s pretty clear that ditching seals altogether could help us reuse engines more effectively, as they’re potential failure points when it comes to reusability.
And get this: without the need for seals, your margin of error in design gets a nice little bump. This makes for a better and more reliable rocket. As we talked about earlier, the Raptor does have more potential failure points due to twice as many turbines. But you also lower the risk of catastrophic failures, like exploding pumps from leaks. Plus, you get redundancy without needing a crazy seal system.
The superiority of the Raptor engine over other rocket engines
By now, it’s obvious that the Raptor engine is miles ahead of its predecessors. But we’re not done yet. Let’s crank it up a notch and compare SpaceX Raptor engine specs to other rocket engines.
One engine that really grabs my attention is the RD-170. This Soviet-era liquid-fuel rocket engine made its first flight in 1985. It was one of the first rocket engines to use staged combustion and was often called the,
“Most powerful rocket engine in the world.”
The Soviets designed the RD-170 to lift super-heavy launch vehicles into orbit. And for a long time, this engine held the record for the highest produced chamber pressure. So when you check out the comparison tables, keep an eye out for this trailblazing, one-of-a-kind engine.
Rocket engine | Power cycle | Fuel type | Chamber pressure |
---|---|---|---|
Raptor (developed by SpaceX) | Closed (full flow) | Methane | 33 MPa (4,786 psi) |
RD-180 (developed by NPO Energomash) | Closed (oxidizer-rich) | RP-1 | 26.7 MPa (3,870 psi) |
RD-170 (developed by NPO Energomash) | Closed (oxidizer-rich) | RP-1 | 24.52 MPa (3,556 psi) |
RS-25 (developed by Aerojet Rocketdyne) | Closed (fuel-rich) | Hydrogen | 20.64 MPa (2,994 psi) |
Merlin 1D (developed by SpaceX) | Open (fuel-rich) | RP-1 | 9.7 MPa (1,407 psi) |
The chamber pressure produced by the SpaceX Raptor engine is nothing short of jaw-dropping. Add in the fact that the engine will experience less wear and tear, and it’s a no-brainer that it’s set to be a game-changer.
Now, let’s take a gander at the produced thrust of these engines. The crucial factor here is the thrust-to-weight ratio. The higher this number, the heavier the payload a rocket can lift into space. So it’s no wonder Elon wants to use the Raptor engine for Starship’s mission to Mars.
Rocket engine | Total thrust (sea level) | Thrust to weight ratio | Specific impulse (sea level) |
---|---|---|---|
Raptor (developed by SpaceX) | 2.21 MN | 200:1 | 330 seconds |
Merlin 1D (developed by SpaceX) | 0.85 MN | 158:1 | 311 seconds |
RD-180 (developed by NPO Energomash) | 3.83 MN | 78:1 | 311 seconds |
RD-170 (developed by NPO Energomash) | 7.25 MN | 75:1 | 309 seconds |
RS-25 (developed by Aerojet Rocketdyne) | 1.86 MN | 73:1 | 366 seconds |
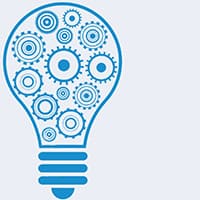
Important Note: Every tiny rocket advancement counts. Even a 1% boost in velocity, considered over the entire length of a launch, is massive. Given the 25,000 miles per hour needed to escape Earth’s gravity well, any increase in velocity will make a real difference in your fuel requirements.
Conclusion
And there you have it—the SpaceX Raptor engine, in all its glory.
I don’t know about you, but I think it’s an amazing time to be a space enthusiast. The advancements of the SpaceX Raptor engine are a testament to the new frontiers waiting for us to explore.
Sure, the Raptor engine is still a newbie in the rocket engine realm. But it’s quickly maturing and is well on its way to becoming the top choice for taking us to Mars someday.
In the meantime, there’s still work to be done on cost, reusability, and reliability. But we can still appreciate the intricacy and fascination these engines offer. Let’s not forget, every new engine advancement further showcases human ingenuity. So I’ve gotta give a shoutout to all the engineers who’ve worked on this fantastic engine.
And honestly, I can’t think of a better company to lead the charge than SpaceX. They iterate and test at breakneck speed, making any necessary tweaks without any fuss. So I have no doubt, not even for a second, that the SpaceX Raptor engine will become a cornerstone in rocket engineering.
So what do you think about the SpaceX Raptor engine? How do you believe the Raptor engine will revolutionize the rocket industry? What’s the next big leap in rocket technology?
Featured Image Photo Credit: Brandon De Young (image cropped)