Simple engineering solutions might not be in-your-face obvious, but they can save you heaps of cash and loads of future headaches.
As an expert, you’ll stumble upon a gazillion possible fixes for every problem that pops up. The real challenge? Choosing the winning solution while juggling factors like:
- Cost
- Feasibility
- Build time
- Functionality
- Reliability
- Complexity
- Serviceability
Sounds like a lot, I know. But that’s why simplicity is the golden ticket to the best possible product. Einstein himself said it best:
“Everything should be made as simple as possible, but not simpler.”
Now, don’t get me wrong, you don’t want to oversimplify and miss your design goals.
Finding simplicity in engineering solutions isn’t a walk in the park
Simple designs are anything but straightforward. In fact, they can be way tougher to come up with than complex designs.
Picture this: you need to mount a device on your home wall. You could just hammer 100 nails into the wall and call it a day. Or, you could figure out the best way to support the load on the wall. After some digging, you realize that 3 large, strategically placed wall hangers will do the trick, instead of 100 nails!
That 100-nail approach would not only drive your spouse up the wall (pun intended), but it’d cost more money. Plus, imagine the nightmare of moving the mounting location later on.
The same lesson from our little example applies to real-world engineering. I’ve seen my fair share of wonky design implementations that give everyone a headache.
My advice? Don’t just jump at the first solution that comes to mind. A quick and dirty fix might make your life easier, like hammering 100 nails into the wall, but it’ll create a world of hurt for everyone else involved.
Give every engineering solution a proper once-over
Before you lock in a solution, take a good, hard look at every aspect of your design idea. Ask yourself these questions about your design:
- Will the solution create problems for consumers and operators down the line?
- Will future maintenance be a breeze or a total pain?
- How will the bigwigs at regulatory agencies see the design?
- Will the implementation of the design bust the project budget and stretch the build time?
- Can the design be simplified even further?
For example, I was designing new EV charging stations for a multi-story parking structure. We had to route power conduits from the switchboard in the basement to the chargers on the fifth floor.
The client wanted to drill straight through the concrete floors to route the conduits. It seemed simple and cost-effective on paper, right?
But this is where you need to slam the brakes. Let’s revisit those questions we asked above.
If you’re familiar with California building departments, you know they’re sticklers about submittals. They want to see every single retrofit structural detail with supporting calculations. And often, it’s for good reason. They want to ensure you don’t compromise the structure. The catch is…
This would require digging up existing structural as-built drawings, assuming they even exist. Then, we’d have to run a bunch of costly structural tests. In the end, this would turn into a massive structural design effort, and it’d be anything but simple. So, we had to scrap that idea.
Instead, I suggested using the existing pipe chases for the conduit routing. This is the area where the existing conduits already run from one floor to the next.
The cost of materials doubled since the pipe chases weren’t close to the chargers. But we saved tens of thousands of dollars on unnecessary structural work. Plus, the building department submittal process was smooth sailing.
Complexity makes troubleshooting a nightmare
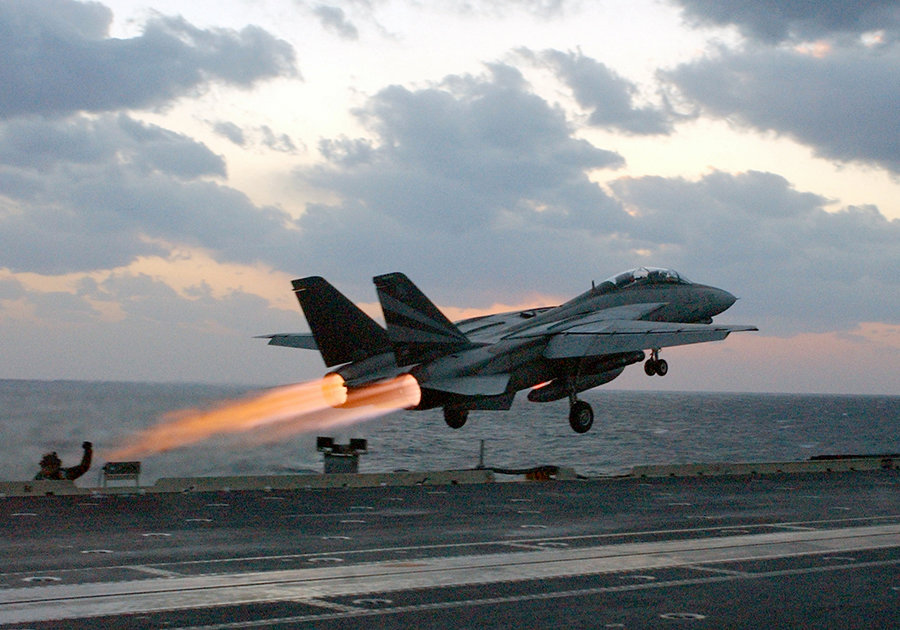
If you’re old enough to remember, you know how hassle-free older cars were. You could easily push a car past 250,000 miles with minimal maintenance.
But nowadays, many cars have all sorts of issues fresh off the lot. One big reason is complexity. There are just so many moving parts and electrical connections, which means more potential failure points. Naturally, repairs become pricier due to increased troubleshooting.
An even crazier example is the F-14 Tomcat. Yup, the badass jet Tom Cruise flew in the blockbuster movie Top Gun.
The maintenance costs for this jet alone were astronomical. In fact, the life-cycle costs of maintaining the jet exceeded its $38 million price tag. It was also the U.S. Navy’s most expensive aircraft to operate, requiring 40 to 60 manhours of maintenance per flight hour. All because of complexity, especially from the airframe. Those awesome-looking sweeping wings were a maintenance disaster.
No wonder the Navy retired the jet early.
What about overengineering in designs?
Sometimes, designs are overly complex out of laziness. Other times, an engineer may lack the experience or know-how to create simpler designs. But occasionally, overengineering plays a part.
Let’s revisit our car example. What if we could add a bed, video game console, and microwave to the car? Or even better, slap on wings to make the car airborne. Whenever LA’s 405 traffic becomes unbearably crazy, you just spread your wings.
But ultimately, a car’s main purpose is to transport you from point A to point B on the highway.
So you only need doors to hop in and out, an engine to move you, and pedals with a steering wheel to help you drive. That’d be my idea of a perfectly engineered car. I’d take it any day if it gets me from A to B without leaving me stranded. All the other fancy bells and whistles? I can live without them.
Often, I see overengineering from folks who aren’t challenged enough or from inexperienced engineers. If you’re in the latter group, learn to meet project specs while keeping your design as simple as possible. In fact, creating a simple design is a challenge in itself.
Make simplicity your go-to in your design criteria for all projects
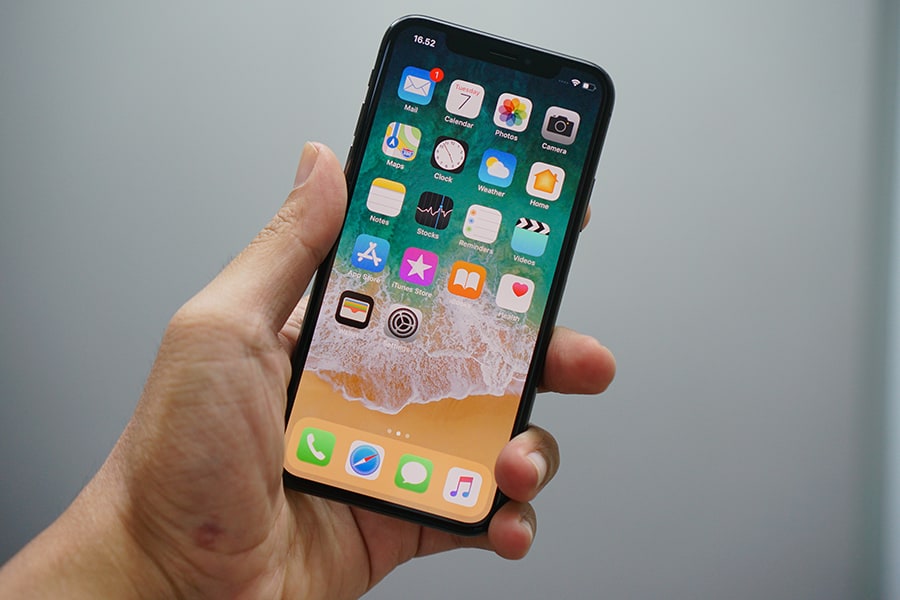
“It takes a lot of hard work,” Steve Jobs said, “to make something simple, to truly understand the underlying challenges and come up with elegant solutions.”
Way back in 1977, Apple’s debut marketing brochure stated,
“Simplicity is the ultimate sophistication.”
No wonder Apple devices are such a hit! Their simplicity is a major draw, but it often gets overshadowed by their jaw-dropping hardware.
Truth is, we don’t usually dwell on Apple’s simple designs because their devices are just that good.
So, take a page from Apple’s playbook and create straightforward products without sacrificing functionality. Treat it like you would public safety – a top priority in any kind of engineering.
Conclusion
Put yourself in the shoes of a builder, manufacturer, or end user. What would you want from a design? You guessed it, simplicity!
As an engineer, always strive to deliver what you’d love to see yourself. If not, you’re only setting the stage for a world of pain when the next person takes over. And that’s just bad engineering!
What are your thoughts on simple engineering solutions? Do you think engineers can simplify a lot of today’s designs?
Featured Image Photo Credit: Bagus Hernawan (image cropped)