Construction management can be downright grueling. But, by using 16 proven construction management tips, the work becomes easier.
From my time as a lead engineer and construction manager, I’ve learned the ins and outs of the industry through a mix of successes and failures. Now, I’m here to help you streamline the management of all types of construction projects, big and small.
#1 Embrace cutting-edge software and hardware
The construction industry is constantly evolving, so why not make the most of the latest tools to boost your workflow? For example, construction managers are often bogged down with repetitive tasks. By utilizing software, you can automate these tasks and cut back on overhead costs, reducing the need for extra staff.
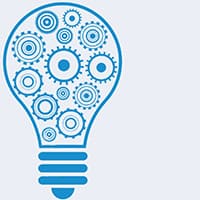
Important Note: Ensure all your staff uses the same software tool to maintain a consistent workflow across the board.
#2 Keep safety front and center
Let’s face it, safety can sometimes take a back seat on construction sites. People get complacent, and cutting corners saves money. But take a look at these 2019 U.S. workplace OSHA stats:
- 15 workers die every day on average
- 2.8 workers per 100 get injured or fall ill
And here are the top causes of fatalities in U.S. workplaces, according to OSHA:
Cause of Fatality | Fatality Source Percentage |
---|---|
Falling from unprotected sides/holes, and poor construction | 36% |
Struck by swinging, falling, or misplaced objects | 10% |
Electrocution | 9% |
Caught in or between machines, devices, or tools | 2% |
Safety must be your top priority, always. It’s not just a legal responsibility; you don’t want someone getting hurt on your watch. The weight on your conscience isn’t worth it. The good news is that you can prevent many accidents by:
- Conducting a construction site hazard analysis before starting work
- Requiring worker safety training
- Using only code-compliant equipment and devices
Also check out my 12 construction site preparation tips to learn how to plan and maintain a safe site!
#3 Stick to your contract
I remember this one time when I, as the lead project engineer, found myself butting heads with a sneaky construction manager. This guy deliberately kept me in the dark about a pricey product submittal, and instead of using the contract documents, he went straight to the vendor with instructions. The vendor began manufacturing, and the contractor only sent me a submittal later to cover his ass.
Normally, a contractor should hand over the engineer’s specs and drawings to a qualified vendor like a baton in a relay race. Then, the vendor compiles a submittal package based on the engineer’s documents. Only when the engineer gives the green light to the submittal does the vendor kickstart the manufacturing process.
Now, back to my story. The moment I received the submittal, I shot it down because it didn’t jive with my design. The fact that the vendor had already started manufacturing didn’t faze me one bit.
The construction manager tried to sway me to accept the submittal, growing increasingly desperate and even irate, accusing me of putting the brakes on the project and burning a hole in his wallet. In the end, his contract-bending shenanigans cost him months of precious time and a small fortune.
So here’s the golden nugget: always stick to your contract like glue. And if you’re thinking of veering off course, loop everyone in right away. Don’t play games with people.
#4 Communicate and communicate fast
A ton of construction blunders can be traced back to good ol’ human errors, with poor communication as the main culprit. That’s why superstar construction managers possess top-notch people skills. Heck, I’d even say it’s a job prerequisite, considering the avalanche of messages you’ll face.
In your role, you should be able to chat effortlessly with these fine folks:
- Clients
- Subcontractors
- Vendors and suppliers
- Engineers
- City and agency reps
- Lawyers and accountants
On the flip side, when messages zip your way, tackle them head-on. Don’t let them gather dust or play a game of hot potato, shuffling responsibilities onto others.
I’ve been on projects where my questions were left hanging for months on end. Then, at the eleventh hour, the managers went into panic mode, scrambling to get me on board because they suddenly had skin in the game. Sure, I lent a hand, but not without a friendly reminder of their earlier brush-offs.
At the end of the day, treat others how you’d like to be treated.
The project manager’s communication pipeline
Set up a sleek, efficient communication pipeline that ensures info zooms to all project stakeholders.
For example, as a subcontractor, I generally won’t reply to direct questions from a construction manager if they’re outside the project’s communication lane. I don’t want to step on any professional toes.
The construction manager might twist my words, or the contractor I’m subcontracted under could blow a fuse about being left in the dark. Instead, I’d forward the question to the appropriate party.
#5 Closely track project budgets
Stay sharp and keep tabs on all project expenses, particularly if your company has underbid a project. In that case, you’ll be tiptoeing on a tightrope, trying to squeeze out any profit.
Keep a keen eye on these project costs:
- Permits
- Wages
- Materials
- Equipment
Statista data shows that even the crème de la crème of projects can exceed their budget, so poor budgeting can haunt anyone.
Project Name | Project Over Budget Amount |
---|---|
Sochi Olympics | 39.00 billion |
The Channel Tunnel | 21.10 billion |
Three Gorges Dam | 16.18 billion |
Boston's Big Dig | 13.45 billion |
London Olympics | 11.91 billion |
Athens Olympics | 6.99 billion |
Denver International Airport | 3.10 billion |
Brazil World Cup | $2.50 billion |
In the same vein, watch over your schedule like a hawk. Because time is money. If a project stretches longer than expected, you’ll bleed money.
#6 Master the Art of Project Meetings and Ditch the Unnecessary Ones
Craft meeting agendas and invite only those who absolutely need to be there. This way, you’ll streamline meetings without wasting anyone’s time.
Sure, large projects tend to have frequent meetings, making them a necessary evil. But honestly, I still think most are uncalled for.
I’ve even had construction managers summon me to weekly in-person meetings. It was not only a waste of my time but also a massive and unnecessary expense for the contractor. Most of the time, the discussions didn’t involve my design work at all. I’d just sit there for two hours, twiddling my thumbs.
For this reason, I tell contractors I’ll only show up in person if I’m absolutely needed. Even then, I’ll ask if I can join via phone call. There’s no way I’m driving four hours or hopping on a plane just to listen to others chat.
#7 Forge Solid Relationships
Building strong relationships starts with kindness and empathy. Of course, sometimes you need to be tough to get things done—some people need a fire lit under them.
But being tough doesn’t mean being downright rude. I’ve encountered construction managers who were blatantly rude for no good reason, thinking their aggression would bend the rules in their favor.
No dice!
In those cases, I’ll do the bare minimum required by my contract and not a smidgen more. If you were kind, I’d even help with tasks outside my scope.
In a nutshell, don’t be an asshole. In return, you’ll complete projects more efficiently and pad your pockets even more.
#8 Mitigate project and construction risks
Top-tier construction managers know every project comes with inherent risks. For instance, consider these scenarios:
- A construction worker on a shaky, elevated platform
- Over-promising a project deliverable to a client
- Ordering from a vendor with lead times that could impact the project schedule
- Ignoring a temporary stream of water and not contacting the local environmental agency
- Skipping a geotechnical analysis before dewatering a construction site
- Receiving the wrong materials from a supplier
Before diving into a project, get acquainted with all the risks. Work out how to mitigate them without compromising your project deliverables.
Also, don’t brush off any risks as trivial just to save a quick buck. If something goes wrong, you’ll face litigation. That’s why this quote rings true for nearly every project:
“No major project is ever installed on time, within budget, with the same staff that started it.”
In short, plan, plan, plan, and be ready to pivot on a dime!
#9 Remain curious and ask questions
If something seems off in the field or office, speak up and ask questions. And don’t be shy about asking questions just to learn.
As a construction manager, you’ll work with various trades, so naturally, you won’t know everything. Plus, the construction industry is constantly evolving in areas like:
- Engineering practices
- Equipment and technology
- Safety and environmental requirements
- Construction codes
Stay in learning mode at all times. Get to know your construction site and the work of the professionals under your supervision. This way, you can catch mistakes before they snowball into massive headaches.
In the same vein, document critical project information. Rather than making a phone call, shoot out an email for the sake of having a record. ‘Cause if things go south, you’ll want to have a paper trail of what went down.
#10 Build an awesome team
As a construction manager, you’re only as strong as the team you stand on.
If your crew is full of lackluster, unskilled workers, you won’t get far. It doesn’t matter how amazing a construction manager you are. So, choose your team wisely and vet each person thoroughly.
And hey, don’t micromanage your workers. For one, it’s just not doable with massive construction projects. Plus, you need to keep your eyes on the prize as the leader. If you don’t, the project will suffer.
#11 Own your mistakes
If you goof up, admit it. In return, you’ll set an example for your team and everyone involved in the project. Plus, you’ll earn the respect of your colleagues.
I’ve seen firsthand how folks follow the lead of an exceptional construction manager. Once a manager takes responsibility for a mistake, others will follow suit. That’s powerful leadership!
#12 Keep a tight schedule
In construction, every single day counts. Time is money, after all.
So, always keep a watchful eye on your schedule. Learn the ins and outs of different project types so you can avoid setting schedules that are too tight or too loose.
Just as important, get to know the different types of project delays. Some are beyond your control, like:
- Owner scope changes
- Labor strikes
- Natural disasters (e.g. floods, fires, and earthquakes)
- Slow decision-making by government or oversight agencies
- Intervention by outside agencies (e.g. environmentalists)
- Site conditions that differ from expectations
- Errors and omissions in contract drawings and specs
Others, though, are within your grasp, such as:
- Late deliverables by suppliers and subcontractors
- Slow mobilization
- Delayed responses from engineers on submittals and questions
- Shoddy contractor workmanship
- Labor strikes due to a contractor’s inability to negotiate fair work practices
- Poor management and planning
#13 Never quit learning
The moment you stop learning, your work starts suffering. Instead, stay hungry for knowledge in areas like:
- New construction software and hardware
- Updated local, state, and federal construction codes and regulations
- Cutting-edge construction practices and methods
Heck, even learn about different engineering disciplines. You’ll only become a better construction manager, and you’ll be able to call out any bullshit by engineers.
#14 Remain patient and flexible
It’s rare for a construction project to go off without a hitch. Something always goes awry. As Denis Waitley once said,
“Expect the best, plan for the worst, and prepare to be surprised.”
I once worked on a project where we stumbled upon artifacts during excavation. This unexpected find halted the project and forced us to redesign around the site. Now, while unearthing artifacts isn’t an everyday occurrence, changes in construction projects are all too common.
So, buckle up and get ready for constant tweaks throughout the process. Keep your cool, stay flexible, and leave some wiggle room in your budget and schedule.
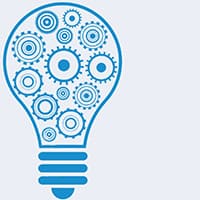
Important Note: Issues pop up in construction all the time. Whenever they do, loop in the entire team. You never know how a change might impact someone’s work.
#15 Become an awesome leader
As a construction manager, you’re the captain of the ship. Keep leading and stay positive, even when the going gets tough. Will Rogers nailed it when he said:
“Even if you are on the right track, you will get run over if you just sit there.”
A big part of leadership is emotional intelligence. Learn to read people, as each person is unique. Treating everyone the same way is a recipe for disaster.
#16 Master the Art of Saying ‘No’
Sometimes, clients will push for unrealistic design changes or unattainable deadlines. In those moments, you need to stand your ground and say “no.” Some changes just aren’t feasible.
Don’t let dollar signs or a seemingly generous client blind you. Remember, change orders come with amended contracts. Fail to meet those obligations, and you could end up in court. Not so appealing now, is it?
The best construction managers I’ve met are straight shooters. They tell it like it is, no bullshitting.
Conclusion
Construction management is no walk in the park, and it can often feel thankless. But with the right planning and these tips under your belt, you’ll knock your projects out of the park.
In the end, top-notch construction managers are worth their weight in gold. They bring life to those lines and numbers on paper.
What are your thoughts on construction management? Which construction management tips do you think are the most useful?