Living underground on Mars might just be our only shot at survival, but that comes with its own set of tunnel-drilling challenges.
So, why do we even need to go underground on Mars?
- Lethal solar radiation
- Freezing cold temperatures
- Intense dust storms
We’d have to make ourselves at home in tunnels, not too different from subways here on Earth. As an engineer, I’ll be diving into the tunneling challenges, specifically in the context of an edge case mission with a mega drill.
But first, let’s delve deeper into Mars’ challenges and why heavyweights like Elon Musk are eyeing the red planet as a destination.
What makes Mars the top pick for colonization?
Check out these factors that make Mars the friendliest spot in our solar system:
- Gravity: Mars has a moderate gravity (3.711 m/s²), similar to Earth’s (9.807 m/s²), making it easier to launch spacecraft from Mars.
- Water: There’s liquid water beneath the surface of Mars.
- Atmosphere: While not like Earth’s, Mars has a thin atmosphere, which is better than the crushing atmosphere of Venus.
- Temperature: Although the average temperature is -81°F, the temperatures aren’t too extreme.
- Distance: Mars is only 33.9 million miles away from Earth, which is close in cosmic terms.
- Martian day: A Martian day is nearly the same as an Earth day, at around 24 hours and 37 minutes.
Let’s compare Mars and Earth a bit more closely:
Comparison metrics | Earth | Mars |
---|---|---|
Diameter | 7,917.5 miles | 4,212.3 miles |
Average distance from Sun | 93 million miles | 142 million miles |
Mass (10^24 kg) | 5.97 | 0.639 |
Surface pressure | 101.3 kPa | 0.5 - 1 kPa |
Year length | 365.25 days | 687 days |
Length of day | 23 hours 56 minutes | 24 hours 37 minutes |
Temperature range | -88°C to 58°C | -140°C to 30°C |
Temperature average | 13.9°C | -62.7°C |
Surface gravity | 2.66 times that of Mars | 0.375 that of Earth |
Surface pressure | 1 bar | 0.006 to 0.007 bar |
Max sunlight | 1370 W/(m^2) | 590 W/(m^2) |
Radiation | 0.62 rads/year | 8 rads/year |
Why is living on Mars challenging?
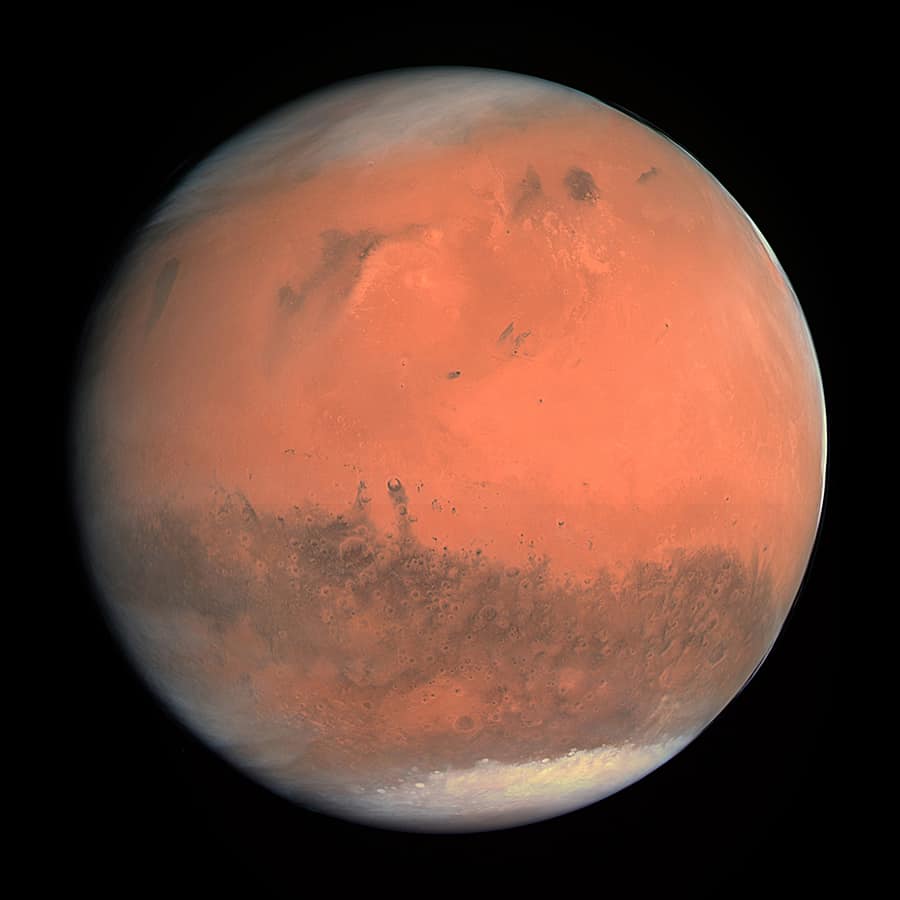
Mars’ thin atmosphere means surface pressure is less than 1% of Earth’s.
One way to tackle this issue is by creating an atmosphere, like sublimating the planet’s frozen carbon dioxide. This could release 12-14 millibars of CO2 and triple Mars’ atmosphere from 6 to about 20 millibars – still far from Earth’s 1,013 millibars at sea level.
Worse still, Mars’ thin atmosphere is 95% carbon dioxide. Check out this table comparing Earth’s and Mars’ atmospheric content:
Atmospheric Composition | Earth | Mars |
---|---|---|
Carbon Dioxide | 0.03% | 95% |
Nitrogen | 78% | 2.7% |
Oxygen | 21% | 0.13% |
Argon | 0.9% | 1.6% |
As you can see, we can’t breathe Martian air – we need way more nitrogen and oxygen.
Mars’ missing magnetosphere
Mars lacks a magnetosphere, the protective shield that fends off harmful solar activity.
For instance, Earth gets bombarded by charged particles from solar winds almost daily. Without our magnetosphere, these particles would gradually strip away Earth’s ozone layer, leaving us vulnerable to dangerous UV radiation. Life as we know it would be impossible without our magnetosphere.
Thankfully, Earth’s magnetosphere does an excellent job of keeping us safe – as long as we don’t get slammed by a powerful Coronal Mass Ejection (CME).
Living underground on Mars – the drilling challenges
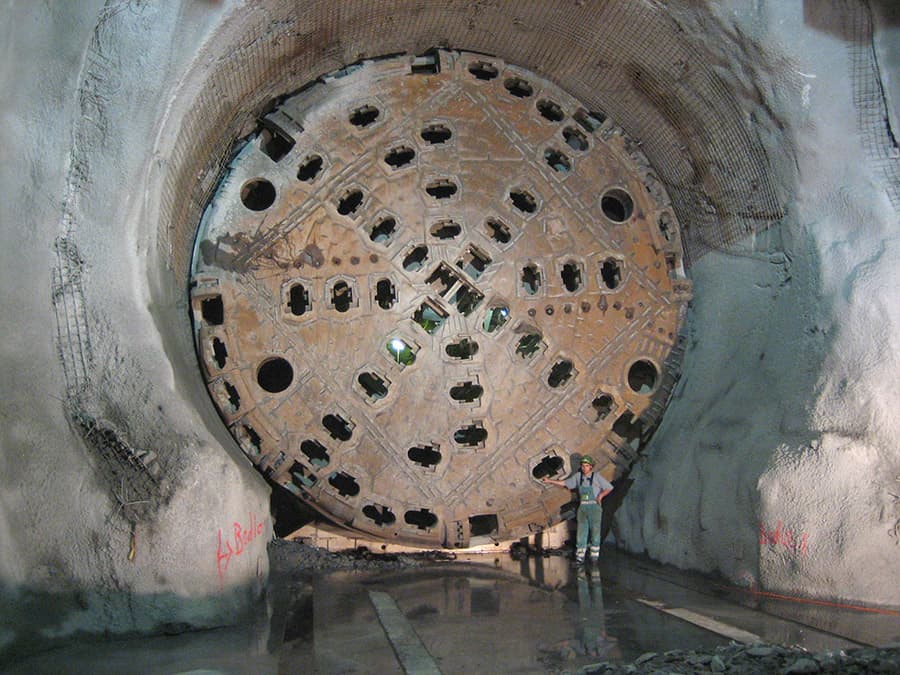
Mars One suggests we’ll need 16 feet of Martian soil to cover our tunnels, providing protection equivalent to Earth’s atmosphere.
My take on tunnel drilling on Mars
Drilling with Tunnel Boring Machines (TBMs) is the go-to method for building tunnels on Earth. However, it’s not without a heap of problems that are rarely talked about.
I’ve been part of large engineering projects where we drilled underground water tunnels ranging from 10 to 40 feet in diameter. Some portions required digging more than 150 feet below ground.
Even with constant oversight, new drilling issues cropped up every week – and that’s here on Earth. I can only imagine what it’d be like 33.9 million miles away in a hostile environment like Mars.
To give you an idea, let’s explore nine drilling challenges I expect we’d face on Mars.
#1 Fixing drills and replacing TBM parts
Drill-cutting bits, like any overused everyday drill, need regular replacement as they become dull. Sometimes, this involves bringing the entire drill to the surface. Other times, the drill breaks down and gets stuck in place. TBM crews then have to go underground and rescue the drill.
But on Mars, who’s going to do the rescuing in a clunky spacesuit?
Sending a mega drill to Mars that can work autonomously seems far-fetched. Good luck trying to free a stuck mega drill without hands-on human assistance.
#2 The power-hungry nature of TBMs
TBMs are notorious for their massive power demands.
In the TBM projects I’ve worked on, each drill needs between 2 and 8 megawatts of power. For a tunnel less than 100 miles long, we’re designing substations at various intervals. These substations have power transformers connected to the grid at 115,000 volts and are rated between 30 to 40 MVA, with some being even larger. The large transformers also feed pumps as large as 5,000 HP to remove underground water.
On Mars, it’s unlikely we’ll encounter water where we drill, so we won’t need massive pumps and supporting pump and motor assembly infrastructure. However, we’d still need enormous amounts of power to run the drill. Where would this power come from? Fusion reactors might be our only realistic option.
#3 TBMs and their snail-paced drilling
Mega drills are painfully slow.
On average, they only drill about 15 miles per year, depending on the underground geological conditions. The maintenance crew’s ability to keep the machine running also affects its performance.
Under challenging conditions, TBMs might only operate 50% of the time. Downtime can be due to various reasons:
- Drilling in poor soil and rock conditions
- Clearing muck from the drill
- Fixing electrical issues
- Managing underground water inflow
- Replacing and repairing worn-out drill parts
- Extending and fixing drill infrastructure
- Waiting for ordered parts
- Addressing safety concerns
The 100-mile tunnel I’m working on has a decade-plus timeline for completion. On Mars, we don’t have that kind of time. We need to get underground ASAP to avoid radiation exposure, which could lead to fatalities and electronic failures. And let’s not forget, each day could bring unexpected problems.
To give you a sense of project timelines, let’s look at some of Robbins’ epic tunneling projects. They’re one of the industry leaders in this field.
Project | Location | Tunnel diameter | Tunnel length | Project timeline |
---|---|---|---|---|
Túnel Emisor Poniente (TEP) II | Mexico City, Mexico | 28.5 feet | 3.6 miles | 5 months |
Grosvenor Decline Tunnel | Queensland, Australia | 26 feet | 1.1 miles | 3 months |
Pinglu Tunnel | Shanxi Province, China | 15.7 feet | 15.8 miles | 4 years 2 month |
The Niagara Tunnel Project | Queenston, Ontario, Canada | 47.5 feet | 6.5 miles | 4 years 8 months |
Boston Harbor Project | Boston, Massachusetts, USA | 26.5 feet | 9.4 miles | 4 years 2 months |
The Manapouri Hydroelectric Project | Lake Manapouri, New Zealand | 33 feet | 6 miles | 2 years 9 months |
Keep these points in mind:
- Number of TBMs: Some projects use multiple TBMs working together. This isn’t feasible on Mars, even though it’s a huge time-saver. Getting one mega drill to Mars is challenging enough, let alone two or more.
- Prep time: Large projects require years of preparation. The Robbins’ project timelines only account for drilling time.
- Challenges: The timeline for these Robbins’ projects could easily triple if the drill encounters unexpected obstacles, slowing progress to a crawl.
#4 The physical size of a TBM
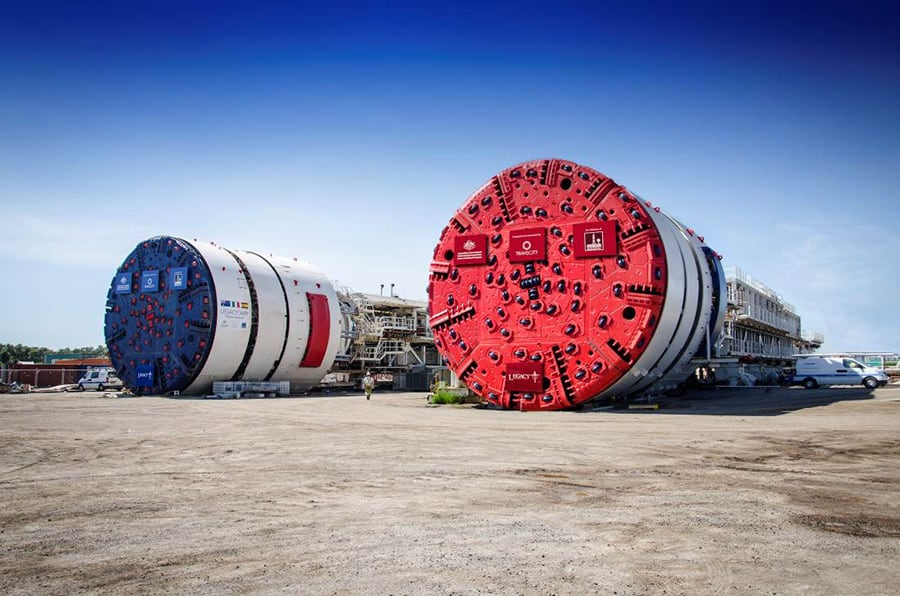
TBMs are not only massive but also incredibly heavy. Sure, we don’t need a 50-foot-diameter tunnel on Mars, but even a 10-foot diameter one would require a gigantic drill.
No rocket today can transport such large equipment to Mars. A sizable TBM weighs over a million pounds and stretches 400 feet long.
Then consider the dimensions of the supporting infrastructure. A 30 MVA 115,000 to 12,000 volts transformer alone weighs about 75,000 pounds.
For context, NASA’s Mars Curiosity Rover weighed 1,982 pounds. SpaceX’s Starship might only transport up to 220,000 pounds.
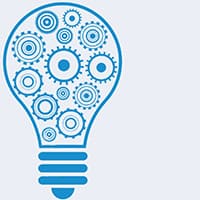
Important Note: Sending preassembled equipment to Mars is preferable. It simplifies life for Martian workers and makes troubleshooting assembly issues easier on Earth than on Mars.
#5 Hauling out excavated soil from the drilled tunnel
We’ve got to get rid of the excavated material from inside the tunnel, which means transporting the dirt and rock to the surface and then relocating it.
On Earth, we move the dug-up soil using large rail cars and typically recycle it in some way.
On Mars, however, this part of the job would be a massive engineering challenge.
Let’s take the Purple Line Extension Transit Project in Los Angeles as an example. It has two 21-foot diameter tunnels stretching 9.1 miles long.
By the end of this project, the TBMs will have cut 495,000 cubic yards of soil. That’s like filling 2.3 million bathtubs with dirt!
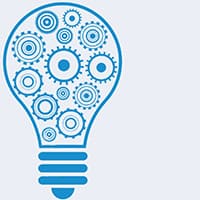
Important Note: Excavated ground is usually mixed with specific compounds to make soil removal easier. So, the 495,000 cubic yards of cut soil ultimately turns into 650,000 cubic yards of hauled-away soil.
#6 Geological drilling challenges
On Earth, contractors always have a contingency plan for any possible issues. On Mars, that’s not feasible since it’s an uncharted land far from Earth’s support.
Here are four geological conditions on Earth that could become major headaches on Mars:
1) Hard abrasive rocks
No matter how tough the cutters are, they’ll wear down over time. If we encounter hard abrasive rocks, the cutters will deteriorate even faster.
Who knows what kind of rock we’ll find beneath Martian soil?
I doubt we’ll be lucky enough to drill through soft soil only. This means we’ll need to replace the cutters frequently.
2) Blocky rock, sand, and clay
These materials and shapes can easily jam a cutter. To tackle these material types, the drill crew uses half strokes with half resets, allowing them to pull back if there’s too much torque build-up.
As a result, drilling slows down, but it’s better than trying to remove a stuck giant drill.
3) Loose running ground, rich in clay
Drilling through this material can cause a collapse above the drill, trapping it underground. Moreover, a large cavity can form above the tunnel where the collapse occurred, possibly extending close to the surface.
To remove the fallen material, engineers sometimes build bypass tunnels, which requires human presence and lots of engineering equipment. The cavity, however, is a major issue since the soil cover served as radiation protection.
4) Underground water
We believe almost all water on Mars exists as ice near the poles.
On Earth, water inflow in tunneling areas is a significant problem. Flooding can cause project delays and damage TBM components.
So, before drilling, operators need to pump out the water in the work area. As I mentioned before, we used several 5,000-plus HP pumps for one of our large drilling projects. These pumps are not only large but also demand extensive electrical infrastructure.
#7 TBM operation’s supporting infrastructure
Along with the TBM, we’d need to bring the following equipment to Mars:
- Electrical gear, such as transformers, switchgear, and nuclear reactors
- Spare TBM parts
- Cranes for lifting heavy equipment
- Hydraulic jacking systems
- Laser-guided gear for directing the drill
- Pre-cast concrete segments for the tunnel’s outer wall
Drilling is no easy task. It requires a ton of equipment and many people working closely together.
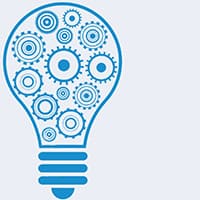
Important Note: Mars has little to no atmosphere, making landing heavy objects on its surface even more challenging. Earth’s atmosphere slows down falling objects, but Mars’ atmosphere doesn’t help at all.
#8 Building a tunnel’s outer shell
As we dig through the ground, we need to install pre-cast concrete panels. These panels form a tunnel’s outer shell, providing essential structural support. Sometimes, though, the panels break or don’t line up correctly.
Such mishaps often stem from inadequate field investigation and geological analysis. The concrete segments may struggle to withstand various tunneling loads, such as:
- Weight of the soil above
- Falling rocks
- Water pressure
- Earthquakes
- Thrust forces from construction conditions
- Wear and tear from usage
On Earth, this analysis can take years. On Mars, we don’t have that kind of time. Plus, Mars is an unfamiliar terrain filled with unknowns.
We definitely don’t want to see failed construction after spending trillions of dollars and countless years. And let’s not forget, creating precast concrete panels is an engineering marvel in itself.
#9 Human team support for a TBM
Working with a TBM is no walk in the park. Usually, there’s a dedicated team of 10 to 15 people hustling and bustling to support the drilling operation since these massive machines can’t fly solo.
On Earth, the human crew faces challenges like:
- 24-hour drilling work schedule
- Extremely loud noise
- Mountains of dust
- Low visibility
- Fatigue
- Dangers of working with heavy equipment underground
- Setting up safety measures
And while we’re lucky to have top-notch hospitals within reach on Earth, over on Mars, there’s no cavalry to come save the day. If you’re seriously hurt, it’s just you and your crew, fighting to survive.
Alternatives to digging manmade tunnels on Mars
As it stands, our tech isn’t quite ready to tackle Mars’ surface with a TBM. But hey, that doesn’t mean we have to abandon our dreams of burrowing into the Red Planet. There are other paths we can explore, like:
- Sealing off natural caves
- Utilizing empty lava tubes
Of course, we first need to find these caves and lava tubes. Once discovered, the amount of digging required will dramatically decrease. And if we pressurize the caves or tubes, we can create Earth-like living environments.
The goal of living underground on Mars
The truth is, terraforming Mars for full-scale colonization is a Herculean task, and we’ve got a long way to go before our technology can catch up.
To be frank, lugging a TBM to Mars sounds like a recipe for disaster. But I have faith that someday, we’ll find a way to call Mars home without the need for gigantic tunnels.
You know, it’s funny—our ancestors started out in caves here on Earth. Now, after thousands of years of progress, we’re looking to circle back and embrace cave living once again…on a whole new planet!
What are your thoughts on living underground on Mars? What do you foresee as the biggest challenges of terraforming Mars? Do you think we should drill our own tunnels into Martian soil?
Featured Image Photo Credit: European Space Agency
Easy to understand, excellent article.
Glad you enjoyed the read.