Substation construction sequencing for retrofit projects requires very careful planning to avoid construction blunders.
I’ll walk you through a recent project of mine where I had the exciting challenge of refurbishing a pair of energized substations. I’ll share the nitty-gritty of the process, the hurdles I faced, and the design strategy I adopted to keep the juice flowing to customers.
Substation project overview
I was tasked with rehabilitating two single-owner-connected 69,000-volt substations:
- Substation A supplies power to Station A via a duct bank
- Substation B supplies power to Stations B and C via a 416o-volt overhead line
These substations were also connected by another 4160-volt overhead line, acting as a backup if one of them failed. Each substation had enough power capacity to keep all three stations running.
With the substations nearing the end of their useful lives, it was high time for a makeover. The outdated equipment was on its last legs, and finding replacement parts was like searching for a needle in a haystack. On top of that, a retrofit would bring everything up to code with current safety standards and regulations.
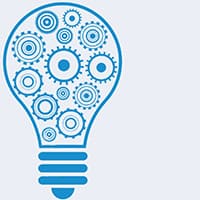
Important Note: People often turn a blind eye to the issue of replacement parts in older, still-functioning substations. They might think their equipment is running like a well-oiled machine and brush off the idea of upgrades. But if a piece of hardware fails out of the blue, it could throw a wrench in the whole system’s operations. Retrofitting new equipment into an existing system isn’t a walk in the park compared to just swapping out identical parts.
Substation refurbishment challenges and constraints
First off, the client didn’t want to cough up extra money for more land. So, I had to squeeze all the construction work within the existing substation perimeter fence.
This made things extra tricky due to equipment clearances. Every piece of electrical gear has specific clearance requirements, and it was like playing Tetris planning the movement of equipment in and out of those tight spaces.
Another challenge was keeping the substations up and running during construction. My client had a bunch of industrial customers who could only afford a few hours of downtime at most.
To top it all off, I had to juggle a few curveballs that could’ve thrown the project off schedule, like:
- Finding nasty mineral oil contamination in the soil
- Delays in equipment delivery
- Contractors not exactly setting the world on fire with their work performance
Design approach discussion
I brainstormed three different design approaches, each of which would affect the substation construction sequencing in its own way.
Approach #1: Construction with de-energized substations
A straightforward strategy was to power down both substations and disconnect the incoming 69,000-volt lines. This would let us safely dismantle the old equipment and demolish their foundations.
The snag? Prolonged outages might last for weeks as we tear down the existing pads and pour fresh ones. And to top it off, concrete pads usually need about 28 days for curing tests.
As if that wasn’t enough, the contractor might unexpectedly hit mineral oil contamination during excavation, throwing more wrenches into our timeline.
Approach #2: Construction with energized substations
The idea here was to build new facilities within the energized substation boundaries while keeping select existing equipment in service.
By “facilities,” I’m talking about substation equipment like transformers and switchgear.
This approach would let station loads stay powered up as we forge ahead with construction.
Approach #3: Construction with de-energized substations and backup diesel power
The plan was to provide backup power to each station when they’re out of commission. Naturally, the stations would operate at a lower capacity during the transition.
This would involve the contractor renting diesel engine generators equipped with in-base fuel tanks.
The price tag for this approach would include:
- Generator units and paralleling switchgear rentals
- Power cabling
- Diesel fuel
- Security barricades for electrical equipment
- Site operators
The cost for this method is hefty, as feeding large loads day after day can quickly drain the budget.
Locking in the design approach
I ultimately chose Approach #2 to minimize outage time.
I designed Substation B to be reconstructed first, keeping its 4160-volt riser structure and switchgear intact. This allowed Substation A to power all three stations. Once Substation B was done, we’d shift our focus to Substation A.
For Substation A, we’d rely on the 4160-volt distribution line connecting Substations A and B. Substation B would support Substation A loads while we took Substation A apart.
After completing Substation A construction, we’d have a brief outage to replace both existing 4160-volt switchgear lineups. Then, Substations A and B would be fully functional and back in business.
Meanwhile, the 4160-volt backup power would be supplied by the utility, sparing the contractor from renting diesel generators. This choice saved us a bundle and nixed a lot of headaches.
Diving into substation construction sequencing
You might not always see it, but behind every well-executed substation construction project, there’s a carefully thought-out plan. As someone with hands-on engineering experience, I can tell you that a creative and practical approach is key to avoiding a world of construction headaches. So, let me give you a glimpse into how I tackled the work sequence for a couple of substations.
Substation B construction sequencing breakdown
#1) Customer to energize the 4160-volt distribution line from Substation A to Substation B.
#2) Customer to open the 69,000-volt main breaker, the 69,000-volt line disconnect switch, and the transformer 4160-volt main disconnect switch at Substation B.
#3) Customer to close the 4160-volt disconnect switch at Substation B connecting to Substation A.
#4) Utility to open jumper at their 69,000-volt pole to de-energize 69,000-volt span into Substation B.
#5) Contractor to install construction fence around 4160-volt riser structure, which is to remain in service at Substation B.
#6) Contractor to begin demolition and construction work at Substation B.
#7) Contractor to request the restoration of utility power with the completion of construction at Substation B.
#8) Cutover of Substation B to utility service, with the utility 69,000-volt incoming span restored and all equipment and facilities installed and tested.
#9) Customer to de-energize the 4160-volt distribution line from Substation A and open the 4160-volt disconnect on the Substation B line.
#10) Contractor to make the connection of the new Substation B facilities to the existing 4160-volt riser structure. Also, connect the existing incoming utility spans to the structure reconnected from the old termination structure.
#11) Contractor to energize Substation B to feed Stations B and C.
Substation A construction sequencing
#1) Utility to de-energize Substation A via 69,000-volt fused disconnect.
#2) Customer to close the 4160-volt switch connecting to the overhead 4160-volt line. The Substation A 4160-volt switchgear will now be back-fed from Substation B.
#3) Customer to close Substation B’s 4160-volt disconnect connecting to Substation A.
#4) Utility to remove span from utility pole to 69,000-volt incoming structure.
#5) Contractor to proceed with demo and construction. This includes the demo of the 69,000-volt structure and supporting equipment, and the main transformer.
#6) Utility to install span from utility pole to new 69,000-volt incoming structure.
#7) Contractor to test and commission transformer and 69,000-volt equipment.
#8) Customer to de-energize the 4160-volt line from Substation B to Substation A.
#9) Contractor to proceed with demo and installation work on 4160-volt switchgear and metering.
#10) Contractor to demo and replace existing 4160-volt Station A feeder cables in existing conduit.
#11) Contractor to re-energize Substation A via 69,000-volt transformer once testing and commissioning of the 4160-volt gear are complete.
“Substation construction sequencing” wrap up
Construction sequencing plays a massive role in large engineering projects. In fact, it can be just as time-consuming as the engineering design itself. One small misstep can lead to costly delays and design failures.
Not to mention, construction staging directly influences the design work. That’s why it’s essential to map out your construction sequencing approach first, creating a solid design roadmap. Don’t underestimate the amount of effort and involvement needed in large engineering projects.
What do you think about substation construction sequencing? What’s your go-to project planning strategy for massive engineering feats?